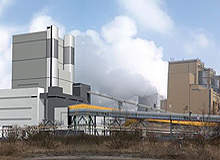
Decision-makers across the power generation industry will be meeting at Arena International’s New Build Europe conference in Germany in May 2010. Key decision-makers will focus on ways to develop and manage strategies for upgrades and brand new power projects.
Efficiency and profitability will be high on the event agenda. Ahead of the conference we look at three case studies where upgrading and boosting technology at three plants – two in Europe and one in the US – is expected to optimise output and enhance lifespan.
Poland’s Belchatow 6: an integrated retrofit process
Boilers and turbines are being simultaneously modernised at the Belchatow 6 power plant in Poland, with major benefits in terms of increased output, efficiency and reliability. After completion of the project next year, the unit can be expected to have another 25 years of productive life ahead of it.
The concept of retrofitting boilers and steam turbines has now become well established as a way of improving the thermal performance and reliability of existing power plants, with integrated retrofit of these major components offering considerable opportunities for innovation and maximisation of benefits.
Over the last 30 years, the technology of coal-fired power plants has made tremendous progress. During this period, the major focus was on turbine aerodynamic efficiency and improved steam conditions. In order to maximise unit efficiency, these aspects will be utilised in the Belchatow 6 retrofit project.
How well do you really know your competitors?
Access the most comprehensive Company Profiles on the market, powered by GlobalData. Save hours of research. Gain competitive edge.
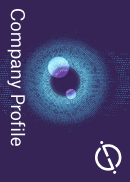
Thank you!
Your download email will arrive shortly
Not ready to buy yet? Download a free sample
We are confident about the unique quality of our Company Profiles. However, we want you to make the most beneficial decision for your business, so we offer a free sample that you can download by submitting the below form
By GlobalDataAs part of an expansion programme, the Belchatow power plant (PGE Elektrownia Belchatow) approved a 25MWe uprating of its unit number 6 and awarded the contract to Alstom Power, the latter being well positioned to offer an optimised integrated retrofit as it has both boiler and turbine capabilities in-house.
As part of the upgrade, most of the main equipment will be modernised, including the boiler, steam turbine, feed heating system and generator.
PGE Elektrownia Belchatow, in the Lodz province of Poland, approximately 170km south-west of Warsaw, is the largest power plant in Poland and the largest lignite-fired power station in Europe. The plant accounts for 20% of the electricity produced in Poland and consists of 12 370/380 MW (originally 360MW) lignite-fired reheat units commissioned between 1982 and 1988 (initially 4,320MW installed capacity, now 4,450MW, following the various modernisation activities completed to date).
The Belchatow power plant was originally developed by the state-owned power utility, but today, as a result of the privatisation process, is owned and operated by PGE (Polska Grupa Energetyczna). Upon completion of a new 858MW supercritical unit and completion of modernisation programmes on ten of the existing units, the installed capacity will be around 5,500MW.
PGE Elektrownia Belchatow is investing in extending the plant’s life, increasing output, enhancing its environmental performance and boosting availability. FGD systems have already been installed on the ten units being modernised and all low pressure turbines have been retrofitted.
In a second phase, Alstom and PGE plan to build a larger plant that will capture CO2 produced by the new 858MW lignite-fired unit currently being built by Alstom. This capture plant is scheduled to be in operation by 2015.
£100m Drax upgrade on target
The UK’s Drax coal-fired power plant plans to cut its annual CO2 emissions by 15% by 2011. This will be achieved by improving efficiency and co-firing biomass materials. Key to the increase in efficiency is the major project to upgrade its six turbines.
The Drax turbine upgrade project involves replacing the high-pressure and low-pressure turbine modules of all six 660MW generating units with modern steam turbines to improve thermal efficiency and therefore reduce emissions of carbon dioxide.
After the turbine upgrade, the power plant, which employs subcritical steam conditions, will operate at an efficiency of around 40%, compared with 38% before the backfit.
Drax’s six turbine generators were originally manufactured by CA Parsons, now part of Siemens. Each of the turbine generators consists of a single-flow high-pressure (HP) turbine, a reheat double-flow intermediate pressure (IP) turbine and three double-flow low-pressure (LP) turbines, exhausting to two pannier type condensers. The five turbines within each turbine generator are coupled together as one single shaft line driving the generator rotor at 3,000rpm.
The upgrade will see the replacement of the HP turbine spindles and static and rotating blading and inner cylinder and the three LP turbine spindles and static and rotating blades of each unit as well as various minor upgrades to enable the new plant to integrate successfully with the existing equipment. In total over 85,000 individual blades are being produced for the retrofit project.
Drax developed a joint agreement with Siemens to ensure that quality control, inspection and hold points were met, to ensure that the challenging manufacturing schedule was maintained. The original turbines are considered part of the UK’s engineering heritage. In February 2010 Drax donated one of the displaced HP turbines and a row of LP last stage blades to the Discovery Museum in Newcastle as part of a project with Siemens and Tyne and Wear Museums.
More rocket science: a CHP that emits no CO2
Effective long-term operation is a key focus for coal-based plants, particularly in the case of integrating fossil and renewable energy to reduce emissions and build towards global targets for a low carbon economy.
A new type of combined heat and power plant, based on the CES oxyburner, is now under development in the US. It aims to be the first commercially viable CHP plant with 100% carbon dioxide capture. This offers a number of advantages over conventional CHP, not least of which is zero carbon emissions.
The technology is the latest concept to emerge from development work on innovative power plant schemes incorporating the CES oxyburner, which has its origins in rocket technology, and is being developed by US-based Clean Energy Systems. The designers, which include Jacobs assisted by other members of the IGSC consortium, envisage that it will be available in sizes ranging from 3MWe to 200MWe, with maximum use of modularisation.
For small-capacity steam turbines, as used in CFHP, commercially available operating temperatures are significantly lower than for utility steam turbines.
In technical terms this means turbines producing 500 to 600 MW, which operate in the region of 600°C. A reasonable maximum temperature for a low capacity steam turbine is 520°C.
At these lower sizes, the power produced is insufficient to make a dedicated cryogenic oxygen plant commercially viable. The amount of power required would take a high proportion of the gross power produced. As a result the preferred solution is based on the use of a storage tank of liquid oxygen regularly topped up by a road tanker. The largest commercially sensible size of a topped-up storage tank is for 100t of oxygen a day which will support a CFHP producing 3MW net of electrical power.
The preliminary design for a larger CFHP plant has been developed, using the new 200MWt CES burner, currently being tested in California. This will require a continuous oxygen supply, likely to come from a dedicated air separation unit, so the design incorporates provision of steam for steam turbine powered drives in the ASU.
Arena International’s New Build Europe 2010 conference will take place on 26 and 27 May in Düsseldorf, Germany.
A version of this article first appeared on Modern Power Systems.