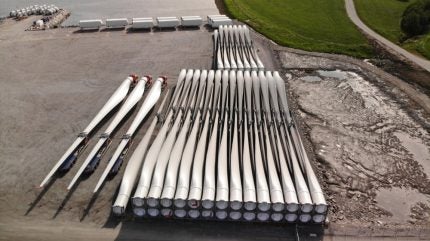
The disposal of wind turbine blades that have come to the end of their working lives is posing an environmental problem for an industry that is intended to help matters.
Made from fibreglass-reinforced polymer (FRP) and coated with epoxy resins, turbine blades are designed to maximise aerodynamicism whilst remaining light enough to minimise structural stress and stiff enough to achieve efficient wind capture.
How well do you really know your competitors?
Access the most comprehensive Company Profiles on the market, powered by GlobalData. Save hours of research. Gain competitive edge.
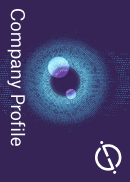
Thank you!
Your download email will arrive shortly
Not ready to buy yet? Download a free sample
We are confident about the unique quality of our Company Profiles. However, we want you to make the most beneficial decision for your business, so we offer a free sample that you can download by submitting the below form
By GlobalDataHowever, the materials are problematic. Having been designed to withstand extreme weather conditions, epoxy resin is durable and therefore difficult to breakdown. The tough coating makes it near-impossible to separate the materials comprising a blade. Separating the fibres from the polymer using high temperatures results in the degradation of the plastic parts and damage to the glass fibres.
Over 317,000 onshore wind turbines are active globally, and there are another 12,000 active offshore, according to GlobalData figures. Since the first windfarm was erected in the US state of New Hampshire in 1980, over 12,600 turbines have been decommissioned. However, that number is set to grow rapidly as many near the end of their 20–30-year lifespan.
The EU’s Waste Framework Directive specifies that landfill is the “least preferred waste management option” and calls for prevention and preparation for re-use, recycling and recovery. With an estimated 800,000 tonnes of turbine blades entering landfill annually, though, there is a serious sustainability challenge to overcome.
Continuum: a mechanical solution
Although a problem for the industry, the issue of sustainable disposal of composite wind turbine blade waste has presented an opportunity for innovators. This includes Continuum, which works with machinery partner Dieffenbacher to convert fibreglass waste into construction materials.
Explaining the company’s approach to Power Technology, Martin Dronfield, CEO and interim chair of Continuum, says: “Using a 100% mechanical recycling process based around a complex series of machines, the ‘front end’ of the process mechanically strips back the end-of-life composite to small particles and constituent parts and the ‘back end’ of the process reconstructs the material with a new virgin resin and transforms it into high-performance, high-value construction panels used for building facades, concrete formwork, doors and floors and wet room wall materials.
“The panel has an CO2 footprint of less than 70kg per tonne, whilst the Zero CO2 emissions factory takes in 36,000 tonnes of end-of-life thermoset composite annually and produces 30,000m3 of high-performance panelling, again annually.”
The company hopes to operate six factories across Europe by 2030, producing infinitely recyclable panels made of 92% recycled blades, with the other 8% comprised of resin. The process is powered by green electricity and produces no emissions, no waste liquids and emits no dust.
Vestas Wind Systems: a chemical solution
Vestas Wind Systems has opted for a different technique, announcing a “newly discovered chemical process” in February 2023. The method breaks down the blades to produce high quality materials, which can be repurposed to make new blades, potentially offering circularity to the industry.
In the announcement, Lisa Ekstrand, the company’s vice president and head of sustainability, said: “Once this new technology is implemented at scale, legacy blade material currently sitting in landfill, as well as blade material in active windfarms, can be disassembled and re-used. This signals a new era for the wind industry, and accelerates our journey towards achieving circularity.”
However, in a review of recycling technologies for FRP conducted in 2023, researchers pointed out that, while chemical processes “are more prone to industrial scalability thanks to the high volume of recycling material processed”, there remains an obstacle – namely “high energy consumption.”
Instead, the review favours mechanical processes for managing waste – such as those used by Continuum – noting that “among the recycling methods treated in this review, the mechanical ones, such as shredding, hammer milling, milling and grinding, are the more appreciable recycling processes to recover glass fibres.”
LM Wind Power: a preventative solution
Considering leaders in turbine blade disposal, GlobaData practice head Mohit Prasad highlights LM Wind Power as a company that “will play a central role in supporting their customers to develop fully circular wind turbines that generate less waste during their production.”
The firm addresses waste at the other end of a blade’s lifespan, aiming to eliminate waste during the manufacturing process. It reports that between 20-25% of materials purchased by wind turbine blade manufacturers are not used in the final product and notes: “Research indicates that blade manufacturing waste volumes are expected to be larger than decommissioned blade volumes in the coming decade.”
Indeed, previous estimates have found that “waste generated during manufacturing and service adds between 16% and 45% of the mass of the wind turbine blades.”
LM Wind Power is attempting to reduce this by manufacturing zero waste blades by 2030. It promises to create a circular economy by eliminating all waste – usually comprising 30% process materials (consumables, mixed with resin), 30% packaging, 15% dry glass fibre, 10% cut offs to composite materials and 15% other, it reports – from the manufacturing process and from packaging.
Polishing a clean industry
Prasad tells Power Technology that the wind turbine industry is already fairly clean, explaining: “85% to 95% of turbine’s materials are recycled. Masts, cables, gearboxes and generators are recycled and recovered. Foundations which are made of concrete are crushed to be used as filler. Nacelles and blades are generally made of fibreglass and are ground down to be used as fuel in cement factories or filler in road construction. Innovative solutions such as repurposing blades into playgrounds or bike sheds have been shown to be effective at a local level.”
However, local solutions are rapidly becoming inadequate. According to the Union of Concerned Scientists, the average blade size for an onshore wind turbine is around 164ft in length, while offshore turbines tend to be larger, with blade spans of up to 260-290ft in length. Repurposing these is not straightforward.
Yet, despite their massive size and landfill requirements, turbine blades are responsible for providing between 120,000 and 180,000 hours of electricity generation in their lifespans, making them a crucial part of the energy transition. Innovation at all stages of the lifecycle by companies such as Continuum, Vestas Wind Systems and LM Wind Power promises to clean up the sector’s waste challenge.