
Algae-fuel is fast becoming a viable green power production solution and alternative to finite fuel sources such as crude oil, which is both costly and harmful to the environment.
However, despite algae’s green credentials and the fact it has several advantages over traditional bio-fuels, such as corn and soybeans, up-scaling of the technology has faced difficulties, primarily due to concerns about the large amount of water it requires.
This issue is once again being debated after new research was published in an American Chemical Society journal which stated that America’s land and water resources could potentially support the growth of enough algae to produce up to 25 billion gallons of algae-based fuel a year, one-twelfth of the US’s annual needs.
The report states that if grown in specific areas where conditions for algae growth are epically favourable, the problem of water is significantly reduced. Many non-renewable power industries rely heavily on water use for production, most notably hydraulic fracking, which has experienced a boom in the US in recent years, so by this comparison, a high reliance on water shouldn’t necessarily hold large scale production of algae bio-fuel back, especially as algae farms can be used to absorb harmful carbon emissions from power plants and other sources.
However, debate continues about the commercial viability of algal power. The Algal Biomass Organization, for example, believes algae fuel could reach price parity with oil by 2018.
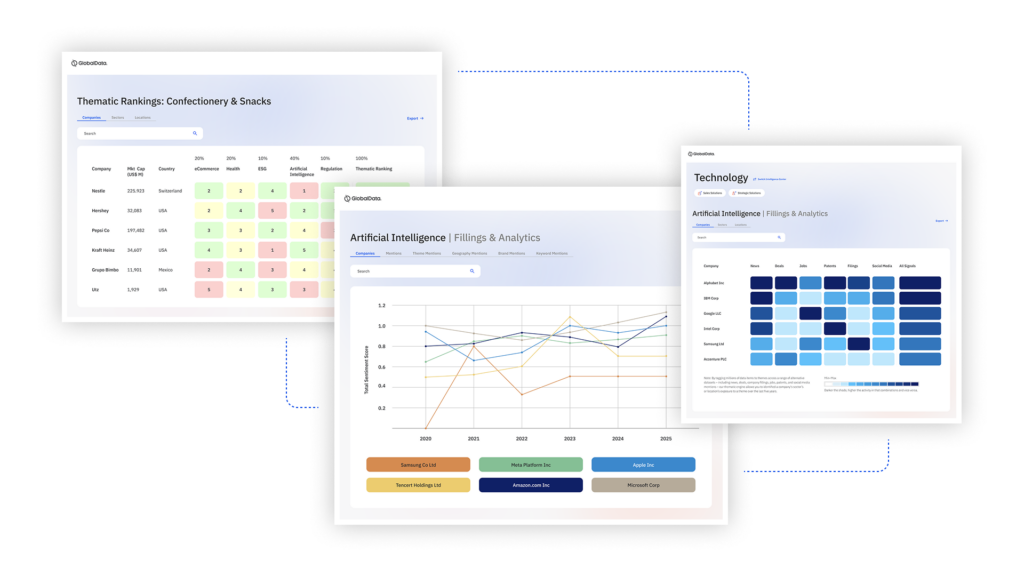
US Tariffs are shifting - will you react or anticipate?
Don’t let policy changes catch you off guard. Stay proactive with real-time data and expert analysis.
By GlobalDataExxon Mobil chairman Rex Tillerson said in March that after spending $600m on the development of algae fuel for the automotive industry it is still probably “further than” 25 years away from commercial viability.
Whichever prediction you choose to believe, there is no doubt algal power production is commanding attention, especially with its ability to be grown in salt-water, fresh-water and wastewater. In time, it’s fair to say, it could be the renewable bio-fuel of choice, especially as its use goes beyond creating bio-fuels for aviation and cars.
World’s first algae-powered building
In March 2013 in Hamburg the ultimate in ‘green’ design technology was unveiled – a building powered entirely by green algae. The building, known as The BIQ house, was created after three years of research and development by Colt International and is based on a bio-reactor concept developed by SSC Ltd, with design work led by Arup.
This first-of-its kind building features 200 squared meters of integrated photo-bioreactors which create a “bioreactor façade” that is mounted as a “second skin” onto the sun-facing sides of the building. Beneath the façade microalgae is cultivated in flat panel glass bioreactors. In total, 129 bioreactors are installed on the south-west and south-east faces of the four-storey residential building.
The photo-bioreactor system generates biomass and heat as a renewable energy resources, as well as providing shade, thermal insulation and noise abatement. The entire unique system is controlled by a fully automated energy management centre, where solar thermal heat and algae are harvested in a closed loop to be stored and used to generate hot water.
Although the building is a prototype of sorts Jan Wurm, Arup’s Europe research leader, believes it could be the next sustainable building solution of the future: “It might well become a sustainable solution for energy production in urban areas, so it is great to see it being tested in a real-life scenario,” he said.
University of Kentucky and UK algae collaboration
Reducing CO2 emissions has been a hot topic ever since the acknowledgment of climate change and power plants are routinely singled out, and often charged, for being one of the worst CO2 emitters.
In a bid to reduce the carbon impact of power plants, researchers from the University of Kentucky Center for Applied Energy Research (CAER) in collaboration with the UK say they have demonstrated a system that uses algae to absorb carbon dioxide emissions from a power plant in Northern Kentucky.
The pilot scale system at Duke Energy’s East Bend power station was built with $1.8m in funding from the Kentucky Energy and Environment Cabinet and the UK, with contributions from Duke Energy.
According to the university, the system works by pumping carbon-dioxide-rich flue gas into a tank full of liquid medium containing tiny, single-cell, plant-like organisms called microalgae. While taking up the carbon dioxide, the algae circulates through a “photobioreactor” — a long course of clear plastic tubes — to absorb sunlight, after which it is returned to the tank and the entire process repeated.
The algae uses carbon dioxide and sunlight for photosynthesis to create the energy it needs to grow, which in these special conditions it does rapidly. The algae is then harvested and turned into sheets, which could be used to make renewable diesel fuel.
“We talk about carbon dioxide as ‘pollution’, but it’s also plant food,” said CAER Research programme manager Jack Groppo. “Algae not only does a great job of capturing and sequestering carbon dioxide, but it also gives us a useful raw material.”
The project is relatively small in scale – less than 1,000 square feet and containing 23,000 litres; however, scientists are currently working on scaling it up in a cost efficient manner.
Overcoming the water barrier
It is possible to reduce the US’s dependence on high-cost oil by using much cheaper algae bio-fuel, a study released in April 2013 from Pacific Northwest National Laboratory (PNNL) claimed.
It was previously thought that although algal bio-fuel is environmentally-friendly and renewable it requires a lot of water. The new study published in the American Chemical Society’s Environmental Science and Technology journal shows that if grown in regions that have sunny and humid climes, such as the Gulf Coast, the Southeastern Seaboard and the Great Lakes of America, it would drastically reduce the amount of water needed to create algal bio-fuel.
After studying previously published data and a comprehensive national geographic information system database that evaluated topography, population, land use and other information about the contiguous US, the team established how much water would be needed and what exact environmental conditions are best to grow algae.
The researchers found that 21 billion gallons of algal oil, equal to the 2022 advanced biofuels goal set out by the Energy Independence and Security Act in the US, can be produced with American-grown algae. According to the study authors, that amounts to 17% of the petroleum the US imported in 2008 for transportation fuels, and it could be grown on land roughly the size of South Carolina. The report found that 350 gallons of water per gallon of oil — or a quarter of what the country currently uses for irrigated agriculture — would be needed to produce this much algal bio-fuel.
It’s worth mentioning that hydraulic fracturing, which is the fracturing of rock by pressurised liquids, for oil and gas is also very water intensive and can use up to 3,800,000 gallons of water per well (Marcellus region, 2009), according to estimates from the US Environmental Protection Agency. Whereas, previously published data indicated conventional gas uses between about 0.09 and 0.3 gallons of water per mile.
The authors of the algae report found that algae’s water use isn’t that different from most other biofuel sources, but that it had significant advantages over other bio-fuels, because it can produce 80 times more oil than corn per hectare a year, and unlike corn and soybeans it isn’t a widespread food source that many people depend on for nutrition. Plus it’s also carbon dioxide-consuming and can be considered a carbon-neutral energy source.
“Algae could be part of the solution to the nation’s energy puzzle — if we’re smart about where we place growth ponds and the technical challenges to achieving commercial-scale algal biofuel production are met,” Mark Wigmosta, lead author and a PNNL hydrologist has said.
The team are now looking at algae grown in non-freshwater sources, such as salt water and waste water, plus green-house ponds, for use in colder climates, as well as economic considerations for algal biofuel production.
Swedish blue-green algae project
Scientists from KTH Royal Institute of Technology in Stockholm announced in March 2013 they were working on producing butanol, a hydrocarbon-like fuel for motor vehicles, from the building blocks of blue-green algae – sunlight, carbon dioxide and bacteria.
Using genetically-modified cyanobacteria, the team linked butanol production to the algae’s natural metabolism.
With relevant genes integrated in the right place in cyanobacteria’s genome, the team tricked the cells to produce butanol instead of fulfilling their normal function. The team have even demonstrated they can control butanol production by changing the conditions in the surrounding environment. This opens up other opportunities for control, such as producing butanol during specific times of day.
Paul Hudson, researcher at the School of Biotechnology at KTH, who leads the research, has said although they are very excited about their discovery: “At the same time we must remember the manufacturing process is very different from today’s biofuels.”
The research needs to be improved “hundredfold” before it can be considered commercially viable, and Hudson says it could be a decade before production of biofuel from cyanobacteria is a commercial reality.
Nevertheless, if commercially scalable it would have significant advantages over other bio-fuels such as corn ethanol, because it requires very little ground space to be prepared and the availability of raw materials – sunlight, carbon dioxide and seawater – is in principle infinite.
Australia also backing benefits of algae
A power plant in Australia plans to take advantage of the carbon absorbing benefits of algae. In July 2013 Algae.Tec announced it had signed a deal with Australia’s biggest power company to site an algae carbon capture and biofuels production facility beside a big coal-fired power station.
The Algae.Tec facility when completed in 2014 will be situated at Macquarie Generation’s 2,640 megawatt Bayswater coal-fired power station in the Hunter Valley, in New South Wales.
The first phase of the A$140m project, which will also produce bio-fuel for the local regions, will feature 400 closed tanks filled with carbon dioxide emitted from Bayswater to stimulate the growth of the algae inside.
The shipping-container sized bioreactors will grow non-GMO algae on an industrial scale for biofuel production to replace fossil fuels. The project is expected to start next year.
Algal oil, a form of vegetable oil, will be converted to biodiesel and hydrogenated to grade A jet fuel at the new biofuels production facility, while waste vegetable matter will be converted into pellets for cattle feed.
The system will also help Bayswater power plant, which is owned by New South Wales government, reduce its carbon costs.
Former Prime Minister Julia Gillard in 2012 introduced carbon pricing, requiring businesses that emit more than 25,000t of carbon dioxide equivalent emissions annually to purchase emissions permits. In July the price of carbon increased to A$24.15 (US$22.27) a metric tonne.
The power plant pumps out about 19mt of carbon dioxide gas a year and the project will capture about 270,000t of that CO2, ramping up to about 1.3mt after a few years.
“Carbon is now our single largest cost. This technology should reduce our carbon output, reduce our carbon bill, and at the same time improve our bottom line,” Macquarie Generation CEO and managing director Russell Skelton said at the time of the announcement.
Image courtesy of Krzysztof (Kriss) Szkurlatowski.
Related content
New report lays climate change blame with fossil fuels industry
A report released on Friday highlights that two thirds of carbon emissions are made by just 90 companies – the majority of which are fossil fuel firms.
Paula Valdés Q&A: breaking the gender mould at Iberdrola
Iberdrola engineer Paula Valdés recently wrote about her experience as Spain’s first female maintenance specialist at a hydroelectric plant.