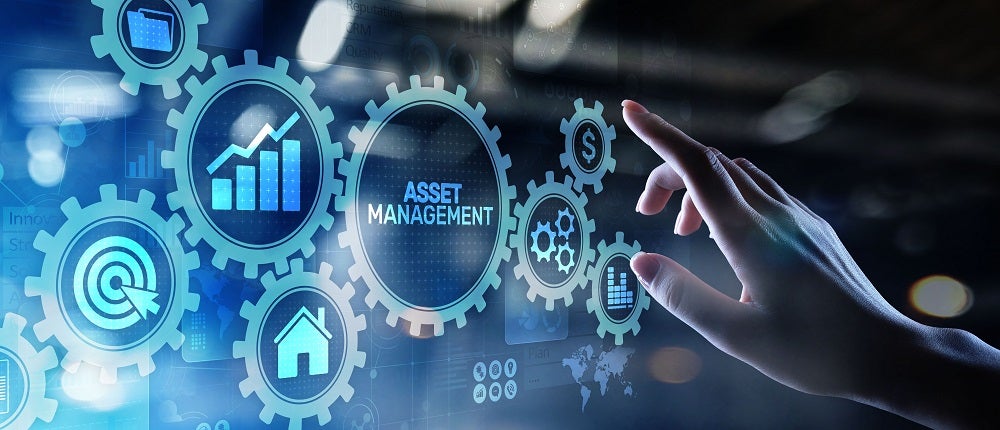
Asset integrity management can be a daunting task, especially when juggling many producing assets at different stages of their service life. Inevitably, assets decay over time, and if an asset does fail unexpectedly it is essential to minimise the impact on production. Most facilities will have a stock of critical spares waiting to replace and/or refurbish older equipment, but just because an asset is not currently being used, this does not mean that it will not also decay over time if it is not correctly maintained.
Crystalise specialises in delivering asset performance improvements to increase reliability, ensure integrity, and optimise maintenance strategies. To understand how companies get the best out of their stock, we spoke with Dr Phillip Tirabosco, principal consultant at Crystalise about managing critical spares.
“The definition of asset integrity is the confidence you have in your asset to meet its safety, reliability, and functional requirements at any stage of its service life,” Tirabosco explains. “These requirements are really what various stakeholders require from that particular asset to deliver its value.
“You have to have the integrity of your producing assets, but also your critical spares. Integrity should be managed across all of your warehousing space, and you have to look at how you are actually maintaining and preserving those spares so that when you do need them, they’re fit for purpose.”
Crystalise helps customers by providing them with an independent inspection to determine the integrity of all their assets, including spare materials that are being stored. Discovering that a critical spare is not in the condition that is required can be disastrous, leading to delays in production so that a new spare can be acquired.
“There’s been examples at various companies that we work with, where they send a replacement pump to the site and the replacement pump is in a worse condition than the pump that is being replaced because the spare was purchased when the asset was new. If it was left in a warehouse, and it hasn’t been maintained or preserved in the right way, then it is not going to work the way that you need it to, and that’s what integrity management is all about.”
“Integrity management has to include critical spares and materials, as well as ensuring that all of the people working at your facilities are properly trained and qualified to correctly operate and maintain your equipment. Integrity management systems cover all those aspects, the people, the plant, and the processes. If something is not quite working right, it gets flagged appropriately so the right people can do something about it.”
Crystalise can provide a structured and auditable process to determine critical spares and stock levels. It is important to note, the number of spares and stock levels need to be just right – too little and it impacts your performance over time, and too much will impact your bottom line. The right balance is dependent on your asset’s requirements, as well as your supply chain restraints.
The management of critical spares is included in ISO 55000, the ISO standard for asset management. Crystalise works with customers to improve current practices by carrying out inspections to help them understand the integrity of their asset so they can prepare an optimised maintenance plan, which ultimately gets the most out of their stock.
For more information about Crystalise and the services that they provide, visit their website or download the whitepaper below.