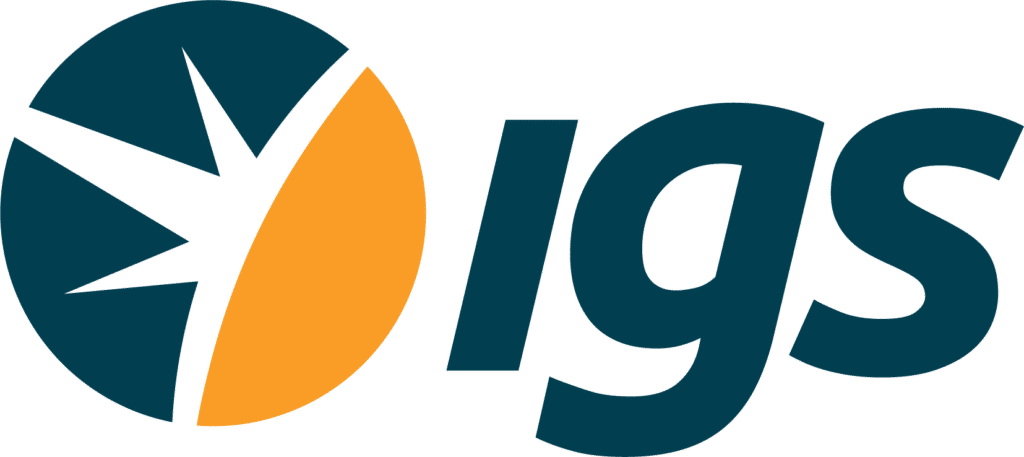
Coal-fired SCR reactors are known to suffer from build-up issues. Though the severity of build-up problems can vary greatly, the causes of and solutions to these issues are remarkably predictable. There are various cleaning methods available on the market that, when used in conjunction with one another, offer SCR owners a comprehensive solution. This article will discuss how each cleaning product, namely LPA screens, air cannons, sonic horns, and secondary screens, works in unison to maintain a high standard of SCR cleanliness.
Large Particle Ash (LPA) Screens: The Foundation
The first and most important step for SCR cleanliness is to prevent Large Particle Ash (LPA) from ever reaching the reactor. LPA is accepted as the primary and most severe root cause of SCR build-up problems. Fly ash accumulation will occur if LPA is present and allowed to reach the SCR reactor.
LPA is generally defined as particles that are 4-7 mm in characteristic dimensions, which can be large enough to lodge within the opening of the installed catalyst. LPA is often larger than the catalyst opening, and if this is the case, the particle will sit on top of the catalyst and prevent fly ash from passing through. Additional fly ash will collect on top of the blocked area and form significant ash piles. LPA can also be small enough to enter the catalyst, but too large to pass through the catalyst. If this is the case, the particle will create a blockage in the catalyst channel and generate build-up on top of the catalyst.
Can LPA formation be eliminated?
Unfortunately, several studies have concluded that the formation of LPA is difficult to predict and virtually impossible to prevent. The best-known defence against LPA is the installation of an LPA screen, which is why all new high dust reactors in the United States and Europe install LPA Screens as original equipment. Several examples can be cited in which vast, LPA-related build-up problems have been solved by the installation of a reliable LPA screen.
The LPA screen is typically installed in the economizer hoppers to prevent LPA from reaching the SCR. If the LPA screen fails and allows LPA to enter the reactor, high operational and maintenance costs are certain to follow. Installing a reliable LPA screen is much like brake pads on a car. They must be replaced regularly enough to avoid catastrophic failure. A reliable LPA screen is critical to the health of all SCRs and is the first step toward a clean SCR.
Other Causes of Build-up
LPA is not the only cause of SCR build-up. Generally, all other build-up problems are caused by poor gas and ash flow distribution. A combination of regions of low gas velocity and high ash loading overwhelms the catalyst and causes pluggage. As the ash covers more and more of the catalyst, the severity of the problem increases. This can lead to some, or all, of the following problems:
- Forced outages for offline cleaning
- A derating of boiler operations
- Shortened catalyst life
- High pressure drops
- Excessive ammonia slips
- Direct negative effect on catalyst performance
To solve problems related to poor gas and ash distribution, SCR owners must install online cleaning systems specifically designed to address these factors. Assuming LPA is kept out of the reactor, data proves that the combined cleaning efficiency of air cannons and sonic horns is sufficient to tackle some of the most severe build-up problems when the cleaning system is designed properly. The secondary LPA Screens are specifically designed to enhance the cleaning efficiency of air cannons and sonic horns, ensuring the maximum effectiveness of the cleaning system.
Air Cannons: The Corrective Agent
When gas and ash distribution are poor, the build-up generally starts along the walls of the SCR (the area with the lowest gas velocity). As the ash piles grow, they reach an angle of repose, causing them to spill out toward the middle of the reactor. This process repeats itself until a small ash pile grows into a sprawling mass of fly ash. The key to eliminating this problem is attacking its source: the small ash pile.
How do Air Cannons Work?
Air cannons are specifically designed to eliminate ash accumulation along the walls of an SCR by addressing poor flow distribution. Each air cannon is a reservoir tank filled with compressed air that is held behind an actuator valve. When the valve is triggered, the stored air erupts through a specially designed outlet nozzle (mounted in the walls of a vessel). The air cannons redistribute the fly ash that accumulates in the high ash loading regions and poor flow zones, sending it back into the higher flow zone in the middle of the reactor. By doing so, the air cannons also re-entrain the ash particles into the flue gas stream, never allowing them to settle, pack in, or solidify. This cleaning action serves as a corrective agent for poor gas and ash distribution problems. Air cannons eliminate large build-up problems by not allowing small deposits to form and propagate.
Air cannons have successfully eliminated build-up in some of the most problematic SCR installations. They are the only cleaning device that directly addresses poor flow problems. All SCRs can benefit from air cannon installation.
Sonic Horns: The Perfect Complement
The corrective agent of air cannons is critical to the health of the SCR. However, their cleaning range is limited to the poor flow zones (about 20 feet from the reactor wall). To guarantee cleanliness throughout the reactor, an additional cleaning device must complement the air cannon. This is where sonic horns come into play.
How do Sonic Horns Work?
Sonic horns use high-energy, low-frequency sound to energize airborne particles and reduce their deposition on layers of catalyst. In other words, the sound waves of a sonic horn vibrate ash particles. Gravity and/or gas flow then filter the accumulation through the catalyst. Although sonic horns do not address poor ash distribution and will become overwhelmed with excessive ash loading, they are very effective at helping a reasonable amount of ash pass through the catalyst. Sonic horns clean a large area and work very well to address build-up beyond the cleaning range of the air cannons. Tests display remarkable cleaning ability from as far away as fifty feet.
LPA screens, air cannons, and sonic horns work together to eliminate problems of poor gas and ash distribution. The LPA screen blocks particles too large to pass through the catalyst from reaching the reactor. Air cannons address poor ash flow distribution and do not allow ash to settle. Sonic horns then help move the remainder of the ash through the reactor and address the hard-to-reach areas. This complementary cleaning system ensures full cleaning coverage for an SCR.
Secondary LPA Screens: The Enhancement
Metal screens have been placed on top of SCR catalysts for decades. The primary purpose of these screens is to enable workers to walk inside the reactor during outages. While these screens generally accomplish that purpose, they offer little protection to the catalyst and present a turbulent cleaning surface that can even hinder online cleaning devices. The secondary LPA screen is the first technological advancement to those initial metal screens. It is specifically designed to offer superior protection to the catalyst and enhance the cleaning action of sonic horns and air cannons.
How do Secondary LPA Screens Work?
Secondary LPA screens offer superior protection to the catalyst by virtue of their material and design. The screen itself is more rugged and better suited to withstand the harsh environment of the SCR. The average perforation size of the secondary LPA screen is much smaller than that of typical metal screens, allowing for maximum filtration while still having a high open area ratio. This prevents chunks of bisect ash from bypassing, reaching, and plugging the catalyst. Whereas most screens only protect the catalyst from being walked upon, the secondary LPA screen offers much more protection.
The secondary LPA screen is specifically designed to enhance the cleaning efficiency of air cannons and sonic horns by using a strategy that is well known throughout the power industry: a smooth surface. This improves the cleaning efficiency of air cannons by keeping the air blast on the screen longer and requiring less force to move the ash. Test studies by Airflow Sciences suggest that this can improve the cleaning distance by as much as 66% while simultaneously keeping the blast away from the fragile catalyst. The smooth surface enables the ash on the screen to move more freely when vibrated by the sonic horn, thereby improving its cleaning efficiency.
LPA Screen + Air Cannons + Sonic Horns + Secondary LPA Screens = Clean SCR Reactor
The causes and solutions to SCR build-up are remarkably predictable once the root causes are identified and understood. When present, LPA is the primary root cause of ash accumulation in the SCR. The first company to offer the full suite of protective solutions is Integrated Global Services (IGS).
Primary LPA screens, air cannons, sonic horns, and secondary LPA screens work in unison to provide a high standard of SCR cleanliness. The combined cleaning efficiency of these products offers customers an unmatched 95% clean SCR guarantee.
Case Study: Supercritical Boilers Suffer from SCR Build-up
A power plant operates four 800 MW B&W supercritical boilers. When Selective Catalytic Reduction (SCR) reactors were installed on units 1, 3, and 4, Large Particle Ash (LPA) screens designed and supplied by a third party were included as original equipment. However, soon after start-up, all three of these units experienced build-up problems in the SCR reactor. The issues resulted in significantly increased operational costs, lost generation revenue ($250,000 per day), and catalyst replacement cost (+ $1,000,000 per layer).
In 2011, a formal investigation into the root cause of the ash build-up within these units, prior to designing the fourth reactor on Unit 2, concluded that LPA reaching the SCR reactor was the primary cause of the build-up. A sample section of the catalyst was cut open and LPA was found lodged deep into the channels of the catalyst with fly ash plugging above this blockage.
A summary of conclusions from the extensive investigation of Units 1, 3, and 4:
- LPA was the root cause of SCR ash build-up.
- LPA entered the reactor because the third-party LPA screens failed.
- The “V-Shape” design increased localized high-velocity zones.
- These localized high-velocity zones caused screen failure due to significantly increased erosion rates.
IGS NoNOxTM LPA Screen
The findings of the investigation prompted the search for other LPA screen options for the new Unit 2 SCR reactor. Based on previous experience, the plant chose to install a NoNOxTM LPA screen manufactured by Integrated Global Services (IGS), rather than the previous supplier. The decision was made based on the flowing factors:
- The NoNOxTM LPA screen minimizes the harmful localized velocities by producing a more uniform flow across the screen.
- The NoNOxTM LPA screen is protected by the longest-lasting, most erosion-resistant cladding material available on the market.
- The NoNOxTM LPA screen minimizes pressure drop by implementing extensive CFD modelling and superior open area ratio of the screen material itself while maintaining the desired filtration capacity.
Reducing Localized Velocity Zones
Velocity is the most significant erosion rate variable due to its exponential relationship with the rate of erosion. LPA screens must be designed in such a way as to minimize flow obstructions that create areas of high velocity or localized high-velocity zones. The restricted flow creates high-pressure regions and diverts the gas stream around the obstruction and into the adjacent gas stream. This phenomenon can increase the localized velocity by three times that of the incoming velocity. Erosion is exponentially related to velocity, therefore three times greater velocity increases erosion rates by a factor of nine or more.
Attention to this phenomenon by minimizing flow obstructions is essential regarding the frame design of the LPA screen. A degree of blockage along the frame is necessary to support the screen, but a quality design can minimize the impact of this by designing the frame and supports to be located downstream of the screen face. This moves the screen material away from the high-velocity regions. IGS Environmental’s proprietary design of the individual screens and their surrounding structures accomplishes exactly that. This design not only minimizes the obstruction but also removes the effects of these obstructions from the screen face, thereby eliminating localized high-velocity zones and extending the life of the screen.
Protecting the Screen with Erosion Resistant Coating
Even after the localized velocities have been mitigated, the LPA screen is in an inherently erosive environment. IGS LPA screen claddings have been analysed by physical erosion rate test experiments, which heat and accelerate typical fly ash particles to impact with a cladded coupon. The erosion resistance of a typical NoNOxTM cladding has been determined to be 40 times greater than that of carbon steel in the same application.
IGS utilizes proprietary application procedures and equipment to provide quality protection to the external and interior surfaces of the hexagonal perforations. Due to the acceleration of the flue gas as it passes through the perforations of the screen material, the internal region is the most critical to protect.
An Economical Design
The design of the perforations also plays a major role in the success of the LPA screen. The perforations must be shaped in a way that allows for the greatest possible open area ratio while simultaneously providing a superior filtration capacity. IGS Environmental accomplishes this by employing hexagon-shaped perforations and utilizing a proprietary tooling process.
IGS has vast experience with using complex CFD technology to design the LPA screen to meet or exceed pressure drop design requirements. A normalized, even flow pattern into and across the screen is the key to this low system pressure drop, which makes the NoNOxTM LPA screen the most economical long-term solution for reliable LPA filtration.
Results and Application
The installation of the NoNOxTM LPA screen in Unit 2 has successfully prevented LPA from reaching the SCR reactor, eliminating the LPA build-up problems that the other units were experiencing. The NoNOxTM screens have been in operation since 2014, and no screen failures have been reported to date.