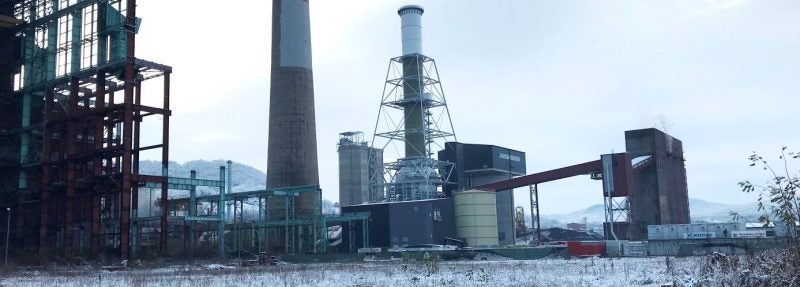
The new plant built by MHPS-E at the RTU thermal power facility in Bosnia and Herzegovina has produced first FGD gypsum.
The commissioning of the desulphurisation plant also initiated the commissioning of the FGD Gypsum silo that ESI Eurosilo completed earlier last year. As the commissioning was very successful, we are finalising the project.
As the Ugljevik thermal power plant dates back to 1985, the outdated environmental safety standards of the power plant needed major improvement to comply with the European standards.
Clean air in a densely populated region is a ‘license-to-operate’ for another 25 years or more. MHPS-E was responsible for providing a state-of-the-art desulphurisation plant that would reduce the emission by 98%. With the new equipment in place, the emission levels have almost reached zero.
ESI project manager Jan-Willem Hanskamp explains: “Integrating a new desulphurisation plant in an existing power plant site means that there is very limited space for logistics solutions to store the produced FGD gypsum. This is one of the main reasons that MHSP-E chose to work with the ESI Eurosilo system in Ugljevik. The all-in-one FGD Gypsum silo integrates dewatering on top, storage with a slotted column inside to reclaim the stored material and truck loading underneath.”
On request of MHPS-E, we have implemented a high level of redundancy in the silo control. The system has a redundant power supply. This is to maximise the availability and to meet the overall power plant standards.
The electrical engineers of ESI investigated and implemented the system into the electrical MCC. The FGD Eurosilo is ready to take on the high output of the desulphurisation plant at the upgraded Ugljevik thermal power plant.