
Renewables are beginning to dominate the energy generation sector, favoured for their low-to-zero carbon emissions and, therefore, the potential to meet climate targets. Though powerful and promising, the unreliable nature of such sources means the industry is increasingly seeking new methods of energy storage.
Currently, lithium-ion batteries are the most popular alternative to traditional lead-acid types, due to their longevity and energy density. However, lithium’s rising costs – going up by 240% in 2017 – coupled with fears over resource depletion, are prompting developers to look elsewhere for low-carbon battery bases.
While possible alternatives have been sought in water, gold, cobalt and sodium, the latest development has come from German conglomerate Siemens, which launched its ‘green ammonia energy storage demonstrator’ on 26 June at Harwell in Oxfordshire, UK.
The demonstrator uses renewable power to make ammonia, a compound traditionally used to boost crop yields, by combining hydrogen extracted from water and nitrogen from air. The ammonia is stored in a tank and converted back into electricity when needed, either through traditional combustion methods or by ‘cracking’ it into nitrogen and hydrogen. In the latter method, the hydrogen can then be used in hydrogen fuel cells to power devices such as electric vehicles.
Crucially, no carbon emissions are produced during the entire process.
The £1.5m project was developed in conjunction with the Science and Technology Facilities Council (STFC), the University of Oxford and Cardiff University.
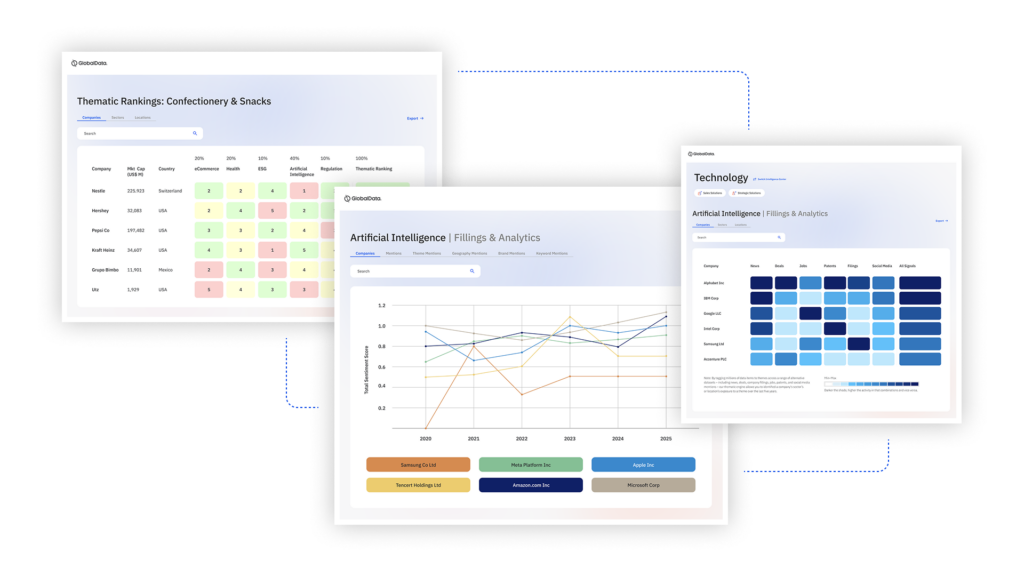
US Tariffs are shifting - will you react or anticipate?
Don’t let policy changes catch you off guard. Stay proactive with real-time data and expert analysis.
By GlobalDataThe STFC contributed to the site infrastructure, the wind turbine and expertise in interfacing with its site and systems, while the University of Oxford helped design the ammonia synthesis part of the system. Cardiff University converted a methane-fuelled generator set to run on ammonia.
Siemens programme manager Ian Wilkinson says the company’s interest in ammonia is partially driven by the fact that “it is based on mature technology and is therefore rapidly deployable at sufficient scale to be useful in meaningful decarbonisation”. Having an existing ammonia industry ensures there is infrastructure in place to store, transport and handle the compound safely from the offset.
“Because it can be deployed at scale and is relatively easy to transport, ammonia energy storage is likely to be advantageous in situations where you need to store a large amount of energy (i.e. high-capacity applications) and/or want to transport renewable energy a long distance (e.g. over a sea),” Wilkinson said.
While current methods of ammonia production use natural gas or other fossil fuels to provide energy for the synthesis process, the Siemens demonstrator gets its hydrogen supply from water electrolysis and extracts nitrogen from the air, with the two elements then combined in the Haber-Bosch process to make the compound.
According to Wilkinson, “current ammonia production methods account for approximately 1.6% of today’s global CO2 emissions”. The company estimates that in its use of renewable energy, its demonstrator could potentially save more than 40 million tonnes of CO2 in Europe alone, and more than 360 million tonnes globally.
The existing ammonia market is huge with around 180 million tonnes produced each year, and the firm has said that this new ‘green’ ammonia could be applied in the same manner as traditional forms, such as in fertilisers, plastics and food processing.
Another possibility lies in extracting hydrogen from the ammonia, says Wilkinson, as it could act as “a practical hydrogen vector and therefore an enabler for a viable hydrogen economy”, perhaps extending its use to hydrogen vehicles. Wherever possible, the hydrogen will be used directly to minimise energy losses inherent in the process of chemical transformation.
The transition would require modification to only some of the existing equipment he says, as “reciprocating engines can run on ammonia with little modification”, though gas turbine engines would require modification to their fuel and combustion systems.
Ammonia has been used as a fuel source in the past, for instance in municipal buses in Belgium in the 1950s, in the Nasa X programme, as well as in various automotives such as the Marangoni / Toyota Eco Explorer. As such, it is already relatively well established as a fuel source, though this is the first time it has been created in a zero carbon process.
Are there any negatives to ammonia batteries?
While gas-turbine combustion techniques fuelled with ammonia do not produce any carbon dioxide, the presence of nitrogen in the fuel carries the risk of nitrogen dioxide and nitric oxide emissions – classed together as nitrogen oxides (NOx).
Nitric oxide itself is not hazardous at ambient concentrations; however, nitrogen dioxide is an irritant gas that causes inflammation of the airways in high concentrations. As such, the safety of the process has come under question.
Despite such doubts, Siemens seems confident that this risk can be easily remedied. According to Wilkinson, researchers at Cardiff University have already proven that a richer air/fuel mixture can significantly lower the NOx emissions, claiming it is more an engineering problem “rather than one of fundamental research”.
“Ultimately, of course, it is possible to scrub NOx from flue gases using,” he says, “for example, SCR [selective catalytic reduction] techniques which are commercially available today. And the reagent used in SCR? Ammonia (or a derivative thereof, such as urea), of course.
Since the demonstrator’s launch, Siemens has been working to commission the system and is expected to share results from the project in due course.
If successful, the project would provide huge gains to the firm considering its production of electrolysers, which use electricity to split water into oxygen and reap the resulting hydrogen as a building block of ammonia. Additionally, the success of ammonia batteries stands to benefit the energy storage and production industry as a whole by providing a reliable and sustainable means of accessing clean electricity.