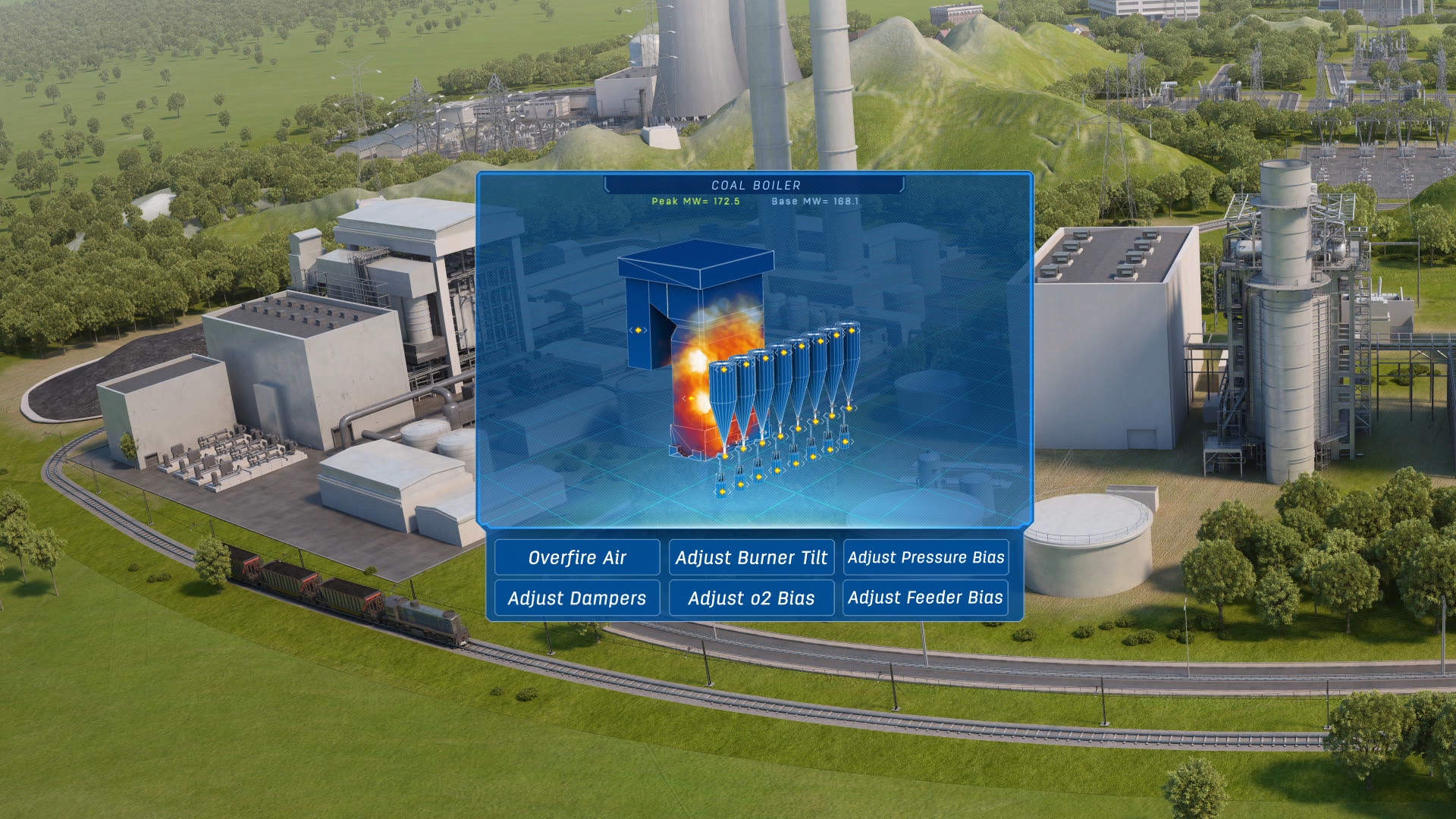
While it’s clear that coal’s twilight era as an energy source has arrived, its pre-retirement period may well be longer than many would like. Persistent issues around renewable intermittency, the complexity of emerging storage systems and growing global energy demand (set to rise by 48% between 2012 and 2040, according to the US Energy Information Administration) means that many countries will continue investing in coal-fired generation for decades to come. India, for example, is committing strongly to renewables but also plans to build hundreds of new coal plants to provide reliable, dispatchable power and fuel the country’s expanding industrial economy.
As concerning as it is for the earth’s atmosphere, coal has got legs in the global market. But what can modern coal-fired facilities do to differentiate themselves from the plants of the past? Increasingly stringent environmental regulations and growing renewable energy integration mean that efficiency and flexibility are at high on the agenda.
GE Power, a GE subsidiary that operates around 40 power plants around the world, is aiming to show what it can bring to the coal conundrum at the Birchwood Power Facility, a GE part-owned 240MW coal plant in Virginia. Built in 1996 and incorporating some advanced pollution-mitigating hardware such as selective catalytic reduction [SCR] and sulphur dioxide scrubbers, Birchwood Power is now being converted into the Global Steam Plant Innovation Center, a showcase for the company’s digital technologies and what they can bring to coal power plant efficiency.
GE Power Digital senior product analytics leader John McDermott and GE Power Services head of operations and maintenance Terry Schoenborn discuss the Birchwood Power conversion, the improvements that are expected and whether coal is still an energy technology worth getting behind.
Chris Lo: What was the inspiration to use the Birchwood Power Facility as a showcase for modern coal-fired steam plant technologies?
Terry Schoenborn: What inspired us to make Birchwood Power this theme innovation centre was that GE owns 50% of this asset, so obviously there are some advantages for GE to do this. We just took over operations and maintenance of the power plant on 1 May. Obviously our company has positioned itself digitally as well, and as you know, coal in [countries like] the US and the UK, it’s somewhat declining. And there are a lot of challenges with coal. The cost – how does it still stay relevant?
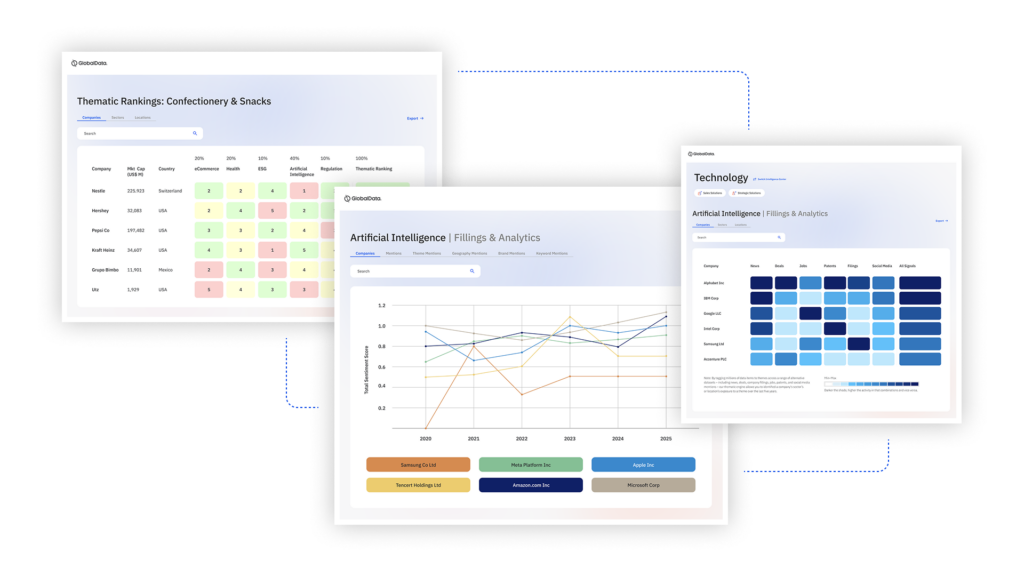
US Tariffs are shifting - will you react or anticipate?
Don’t let policy changes catch you off guard. Stay proactive with real-time data and expert analysis.
By GlobalDataSo the inspiration for us was that we have some ownership of it, we run it, we have this tremendous digital business – let’s put all of the digital technologies that we have on this plant to make it the most efficient, reduce O&M costs, drive heat rate, everything that we can do in our digital arsenal, let’s put it in this plant and really demonstrate the full capabilities and breadth of the company. The thought process is that if we can prove it out here in a very competitive market in coal, then we can take this worldwide as well, in other countries like India and China and the like, where coal still dominates much of the fuel base.
CL: At what stage is this project now?
TS: I would say we’re now in the installation phase of many of our digital solutions. We’ve got four different digital solutions that we’re installing. One of them is asset performance management [APM], and we expect that to be fully implemented by September. Another solution we have is operations optimisation software, which is really boiler optimisation software, and we expect that to be fully implemented by the end of October. By the end of the year we should have all of our digital solutions fully installed, fully tested, and then really getting the preliminary review of some of the benefits.
We’re targeting anywhere between 0.5-1.5% heat rate improvement, so that will obviously save on the fuel. We’re also looking at probably a 10-15% emissions improvement, and if we optimise emissions, this plant has an SCR so we can save on ammonia. As far as O&M costs, we’re looking at probably 15% [savings] over the next five years on the O&M costs.
CL: What do you consider to be the core fundamentals of how a coal-fired power plant needs to operate in the modern power sector?
TS: There’s no doubt that renewables are playing an increasing role in the power mix in a lot of different countries, but 75% of the world’s electricity still comes from the legacy fuel sources of fossil. Our projections are that coal will remain the world’s second-largest energy source through 2030, so coal still has a play.
So what does it need to do? It needs to be more flexible; traditionally coal has been a baseload-type plant. You start it up, run it, you leave it online. And even Birchwood Power has seen a lot of cycling, starting up and shutting down quite a bit. And then also emissions; the world wants cleaner forms of power. It needs to be more flexible, cleaner and emit fewer emissions. This is what a lot of the plant managers and our customers are working to optimise.
CL: How would you respond to those who argue that coal-fired power generation has no place in an environmentally-responsible power market, no matter how efficient, and that ‘clean coal’ is a misnomer?
TS: India is 70% coal today. Renewables will make a play, but it won’t be anytime soon that countries like India will move off of coal. We feel it’s our responsibility to really make coal as clean as possible, and there hardware solutions like scrubbers to reduce SO2 and selective catalytic reduction, which reduces NOx. Baghouses remove emissions. But then there are also software solutions.
As we see our role, there are countries that have coal resources, and they’re going to use those resources for their benefit and energy policies. We just need to position ourselves and help them make it as clean as possible. So coal will be here, how do we as a company help our customers make it as clean as possible and make it still part of the mix?
CL: To what extent is digitisation the core component of the most advanced coal power stations?
John McDermott: I think, for a long time, the way to try to get greater efficiency and reduce emissions was to introduce new hardware, and a lot of extremely valuable hardware was invented that both had a very positive effect on efficiency, on reducing CO2, and a very positive effect on reducing NOx and other pollutants. But I think we’re beginning to get to a place where people now see that probably additional improvements are going to rely more and more on software.
Some of the things that are being introduced now are sensors that can provide a lot of information about what’s going on in the plant, but if you give all the data that those sensors to produce to people, it kind of overwhelms them. They can’t just be sitting around looking at vast amounts of data.
So now, if we have a goal of driving heat rate down as low as possible and driving NOx pollutants down as low as possible, we can then look at the relationship that these new instruments help us, and based on that information we can operate the plant in a way that’s more sensitive.
CL: With advanced digital systems, how do you see the nature of O&M technicians’ work changing in the most advanced coal power plants?
TS: As you can imagine, each power plant has something like five shifts of operation, and it’s been my experience that every operator has how they want to set up the parameters, say. They set their things up, and it’s not always optimal. Part of the digital effort is to place the plant in an optimal position all the time, and although you may be removing the operator from doing that, they still can override the system. But then I think it trains them on where the optimal point is, if they didn’t receive the necessary training.
We’ll always need people to run the plants, but I think we’re just giving people more information to make informed decisions. I think that’s the key – digitisation is just giving better information. Do I need to shut the plant down right now; do I need to do it tomorrow? Can I wait a week before I can do it, I’m in the money today during the peak season in the summer; can I wait? I think that’s the value of the digital aspect.