As companies across the world are forced to examine the cracks in their supply chains in the wake of the Covid-19 pandemic, they are also having to reassess where they locate their on-the-ground operations. A total redrawing of the foreign direct investment (FDI) map is a distinct possibility.
“Every client is examining their footprint – where they should manufacture their products, store inventory, source materials from and do their final assembly,” says EY global and Americas supply chain leader Glenn Steinberg. “This is increasing the pressure on supply chains and requires a fundamental rethink of the concepts of supply chain management and supply chain strategy.”
CEO of manufacturers’ federation Make UK Stephen Phipson agrees.
“[Covid-19] has made people want to re-think a lot and there are lots of discussions at the moment about the way supply chains are going to evolve out of this.”
A disruptive environment
This isn’t the first time a crisis has caused companies to re-evaluate their supply chain efficiency. There have been many disruptions even within the past decade – the Tōhoku earthquake and the Fukushima Daiichi nuclear disaster, both of which occurred in Japan in 2011, challenged the ethos of global supply chains. Alongside this, there has been a heightened number of large-scale cyberattacks in recent years and rising concerns over carbon dioxide emissions to contend with, but Covid-19 appears to be accelerating the need for new supply chain strategies.
A component-maker in Germany who wishes to remain anonymous believes that shortening supply chains will be the first strategic move for many companies. He says: “We have a very distributed network, with suppliers and plants scattered across the world. This model is going to go.”
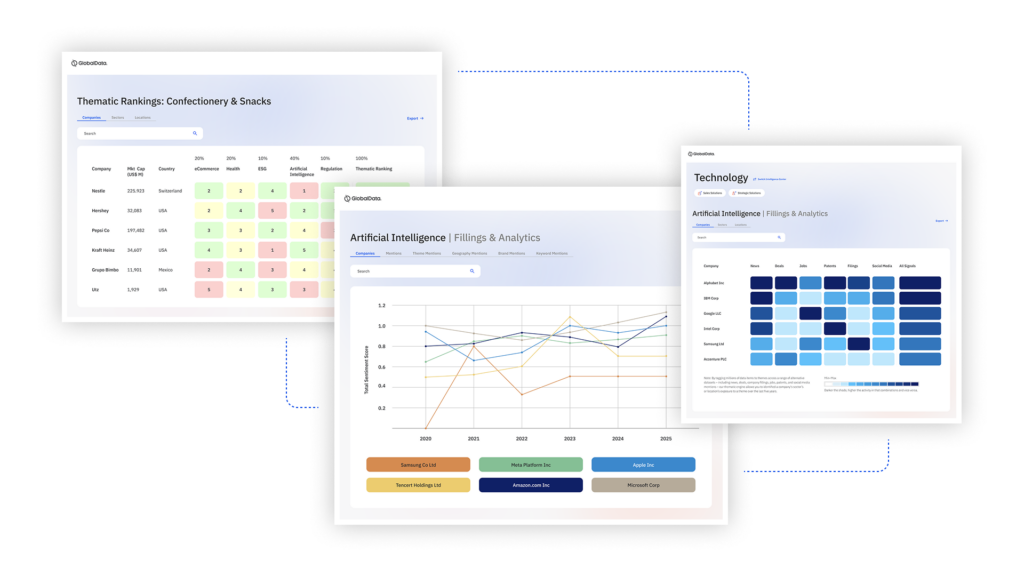
US Tariffs are shifting - will you react or anticipate?
Don’t let policy changes catch you off guard. Stay proactive with real-time data and expert analysis.
By GlobalDataHowever, reshoring is a massive undertaking that forces companies to take many variables into consideration.
Senior partner at McKinsey in Singapore Matteo Mancini explains: “Companies take time to decide where to invest manufacturing capacity, and it is a complex exercise that considers several elements, from safety and the resilience of the supply chain, to overhead costs. If [Covid-19] takes some time to be resolved, some companies will take the opportunity to review the supply chain and make it ‘more local’ where demand is [strong] enough in their local countries.”
Pause for thought
Companies appear to be using this time to examine what has gone wrong in their supply chains and how to side-step these issues in the future. For many, there is a strong focus on diversifying their manufacturing out of China to alleviate their reliance on the country, with many left struggling after their Chinese manufacturers shut down during the onset of Covid-19.
Steinberg explains: “In Japan, the stimulus package released [in late April] included $2bn to help Japanese companies move production out of China and back to Japan, and another $200m was set aside to help move production to other countries.”
This stimulus package, and similar initiatives from other governments, could pose opportunities for locations looking to offer an alternative to manufacturing in China.
China’s loss?
Reshoring would in many cases require companies to evaluate which is more important – cost efficacy or building factories closer to consumers.
Phipson expands on this from a UK manufacturing perspective.
“Reshoring is a tricky thing,” he says. “It is really about making it competitive, and the main challenge we face is that we have spent many years offshoring to Asia and [the region is] very cost-efficient. So, trying to reshore those things and keep the same costing is hard and, as a result, it is really difficult to get businesses to invest in [such moves].
“Until recently, the big emphasis was on cost-efficiency, but now more people are going to start incorporating risk more into their procurement decisions. They are going to look at shortening those supply chains – do they need to have that made in China? Is there another cost-efficient way of doing it? Can we reshore where possible and continue to encourage people to invest in the UK? Also, can we take advantage of looking at alternate sources, even having two sources for something instead of one?”
In advance of the launch of our FDI-focused site, please complete the following survey aimed at investigating how investment plans are changing in the wake of Covid-19.
Your participation is confidential and the survey will take no longer than 5-10 minutes to complete. As a thank you we will share a copy of the survey write up with you.
That is where locations looking for new investment could see a potential win. For many companies, completely reshoring their supply chains is not an option, even when taking into account the heightened interest in protectionism coming from the US and UK. Yet, finding alternative manufacturing locations and additional sources to work as future ‘insurance policies’ does seem to be high on the agenda of these companies. This strategy could not only make supply chains more robust when disrupted but could work to lessen carbon dioxide emission concerns over supply chains that are spread out across large areas.
Future site selection
Markus van Tilburg, managing director of Global Aldea, a site-selection and FDI support specialist, agrees.
“Companies will think about their strategic global footprint in a way that is more than just a low-cost approach,” he says. “Furthermore, companies will carry more local safety stock and extend their supplier networks.”
He is optimistic about the future of site selection and companies’ intentions to continue investing in new locations.
“International business travel, which is vital to site selection, is non-existent right now,” says van Tilburg. “So obviously, there is a huge impact on my work. Nevertheless, most companies are getting prepared for reopening. Many companies have only postponed plans for site selection.”
As eyes start to roam the globe for alternative manufacturing locations, and investment interest in secondary suppliers rises, locations should prepare themselves for the new opportunities that a post-Covid-19 supply chain environment may allow them.