
Once through cooling, simply running the water through heat exchangers is the cheapest option for a power plant if it can be located close to a sea, lake or large river. However, this can divert unacceptable amounts of water and affect aquatic life, both in its extraction and when the higher temperature water is returned to the environment. The temperature of the inlet water must stay below the discharge limit of around 30°C to avoid the plant being closed down in hot weather.
This can make cooling towers a large, expensive but necessary evil. These towers are a plant’s final layer of heat exchange, although they eject heat to the air. The size and cost of dry cooling towers – and the fact that they are not as effective at reducing water temperatures as wet towers – can rule out their use except where water supply is a problem, which leaves wet cooling towers as the most popular choice where once-through cooling is impossible or undesirable.
One issue with wet cooling towers, however, is the plume that occurs when the water is expelled from the cooling tower. With increasing pressure on water supplies worldwide, another challenge is to reduce the water they consume.
Hybrid cooling towers can address both these problems, and because they use mechanical draught they can be much smaller than natural draught towers.
Plume elimination
Although it consists of only water, the plume from wet cooling towers can be huge in cold and / or humid weather.
As well as leading to complaints from local residents, it can corrode nearby components and form ice. This can be dangerous in residential areas or if roads or railways pass nearby.
How well do you really know your competitors?
Access the most comprehensive Company Profiles on the market, powered by GlobalData. Save hours of research. Gain competitive edge.
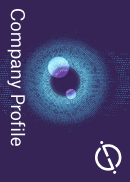
Thank you!
Your download email will arrive shortly
Not ready to buy yet? Download a free sample
We are confident about the unique quality of our Company Profiles. However, we want you to make the most beneficial decision for your business, so we offer a free sample that you can download by submitting the below form
By GlobalDataHybrid cooling towers do away with the plume. These are basically wet cooling towers, but mix the plume with a dry, hot air stream before it leaves the cooling tower. The air expelled is not saturated and the plume is invisible.
Hybrid towers need no extra energy because the air stream is generated in heat exchangers, heated by the water being cooled. The towers are often used in built-up areas and so usually have low-noise fans and sound attenuators.
Separate forced draught fans before the wet and dry sections can be adjusted for minimum power consumption. Accurate control is essential to ensure plume-free operation despite changing weather conditions. The wet section fans control the cooling water temperature, which is determined by the water flow rate and heat rejection rate. The dry section fans control the warm air flow.
Thermal performance of cell-type cooling towers can drop if the plume is sucked back into the air inlets. SPX Cooling Technologies reports that round towers are generally taller and suffer less from this recirculation and interference. Round towers also require less space than large cell-type plants and less piping is needed, because a single hot water pipe leads to the cooling tower rather than allocating a pipe to each cell.
Hybrid towers – similar to wet towers – evaporate a lot of water to the air. SPX has developed a system with a series of PVC heat exchanger packs in the tower plenum that use ambient air to condense much of the moisture before it exits the tower. Air2Air can be retrofitted to a single cell or an entire tower, depending on the required water return rate. Recovered water can be returned directly to the tower basin, or piped away as a pure water stream for boiler make-up or other plant uses.
Reducing water waste
Wet / dry systems also reduce water consumption. These run water and air-cooled condensers in parallel to combine the advantages of dry and wet cooling.
In GEA’s PArallel Condensing (PAC) system, exhaust steam coming from a steam turbine generator is immediately separated into two streams. One stream flows into a surface condenser while the other is directed to an air cooled condenser (ACC). Condensate recovered in the two condensers can be collected in a common hotwell.
The steam distribution between the two units does not need valves or dampers, and water consumption is controlled by the heat load distribution between the two condensers. The system uses wet cooling in the warm seasons, and there is no plume in winter because dry cooling is enough and the wet tower fans can be switched off. The system costs less, and has a smaller footprint and lower fan power consumption than dry cooling towers.
GEA’s system has, for example, been used in the 225MW Afton Generating Station near Las Cruces, New Mexico, US. This had a two-cell cooling tower with two-speed fans. Makeup water for the wet cooling system comes from raw water wells on the Afton site. The warm (27-32°C) well water is cooled before treatment. Here, PAC works in one of several modes depending on the ambient temperature. Fans can be off, or run at low- or high speeds.
At 37°C, all the fans – in both the ACC and the cooling tower – run at high speed. The circulating water then passes through the surface condenser at full flow. As the ambient temperature drops, the fans can run at low speed or switched off. Afton actually runs one circulating water pump during the winter to maintain some water flow through the surface condenser tubing and prevent fouling.
Hybrid’s shorter stature
Another reason for the popularity of hybrid towers is the sheer height of natural draught towers. This is a major factor at Horizon Nuclear Power’s Oldbury plant, and Horizon is opting for hybrid towers because they are typically 70m high rather than the 200m-plus of natural draught towers.
The plant will likely start construction in 2019, and Horizon has said that moving away from natural draught cooling towers has been a big decision. The smaller towers will be more in keeping with the existing Magnox station next to it, and the lack of visible plume will also make the power plant less obtrusive.
Horizon stresses that it has consulted with local residents, but there is still strong opposition to the planned site. Residents of the nearby village of Shepperdine, particularly, protest that their view across the river Severn will be scarred by the cooling towers, even hybrid ones.
Oldbury is the oldest nuclear power station still operating in the UK and residents have been looking out at the existing Magnox station for over 40 years. They say that feel that the proposed 3GW plus station (nearly four times the power of the existing one) is excessive, irrespective of what sort of towers it uses.