
Siemens have successfully load tested 3D printed gas turbine blades, in an important achievement in the development of Additive Manufacturing (AM) in the energy industry. The blades are made of a powder of high performing polycrystalline nickel superalloy, designed to withstand intense testing conditions within the 13MW Siemens SGT-400 industrial gas turbine.
The blades where printed by Materials Solutions and must withstand 13,000 revolutions per minute under immense temperatures. A full load test involves travelling at over 1,600km/h, and carrying eleven tons. The gas surrounding the blades can reach 1,250 °C when the turbine is in full operation.
This isn’t Siemens first use of AM, something they have been involved in since 1989. “Siemens extensively uses AM technology for rapid prototyping and has already introduced serial production solutions for components in the gas turbines’ compressor and combustion system,” says Siemens Power and Gas press officer Alfons Benzinger. Siemens has had 3D printed components in its commercial heavy-duty gas turbines since July 2016.
A significant step for the technology
As the blades are the most challenging aspect of a turbine, the success of Siemen’s full load test opens up many new possibilities.
The biggest benefit of AM is the reduction of lead time, which is cut by 90% for prototype development. This shortens the process from around two years to only two months. “We can accelerate the development of new gas turbine designs with an increased efficiency and availability, and can bring these advancements faster to our customers,” says Benzinger.
Not only does 3D printing ensure that the designs can be built and tested quicker, but it is also cheaper and more flexible than traditional construction.
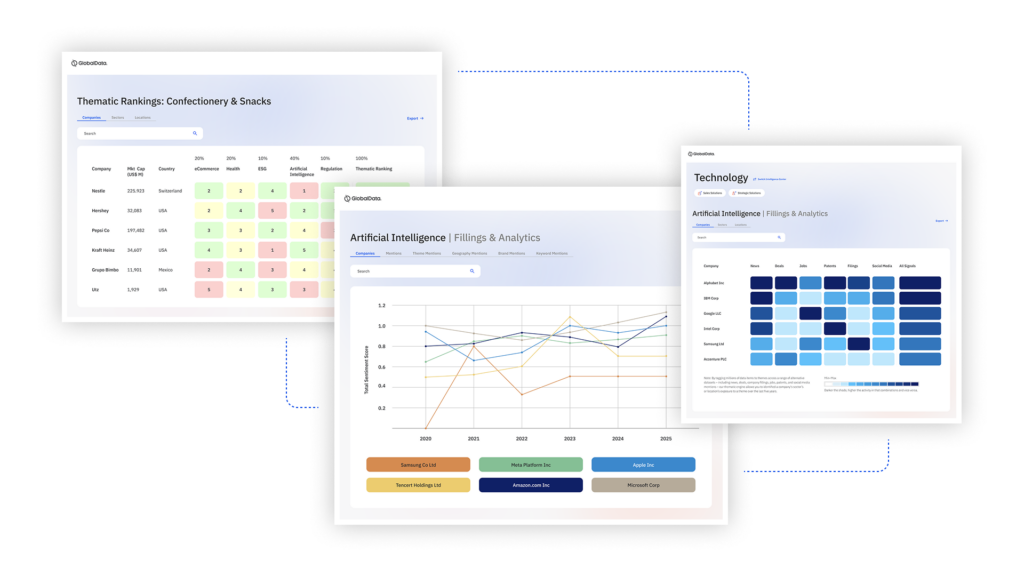
US Tariffs are shifting - will you react or anticipate?
Don’t let policy changes catch you off guard. Stay proactive with real-time data and expert analysis.
By GlobalData“The exciting AM technology allows us to shape and form cooling geometries that weren’t possible with traditional manufacturing technologies,” says Benzinger. “This allows us imagination! It is a real game changer.”
More to come
The faster, cheaper alternative AM provides is a clear winner for Siemens manufacturing, and will be increasingly employed. They are already looking into extending serial production for printed turbine components. Siemens opened a new facility specifically for 3D printing in February 2016 Finspång, Sweden to continue development.
Not only will 3D printing be applied to existing technology but because it provides ease and flexibility to construction Siemens are hoping to use it to develop new technologies. The company is already developing unique gas turbine designs which are only possible with AM.
The success of Siemens test has proved the competitiveness of AM, ensuring that 3D printing will have a big role to play in the future of turbine manufacturing and beyond.