
Although full-scope power plant training simulators are essential for final operator training, they are still very expensive and often not fully ready until the power plant is in service. Design simulators are likewise specialised pieces of software that are often hard to use and may not be fully available until several years after a project has started.
Instead, desktop simulators are stepping in to fill the gap to complement full-scope simulators. Desktop training simulators do not exactly replicate the chosen control room environment but they do show devices such as control board hand-switches and panel devices on monitor displays.
The use of desktop simulators has also expanded to include design optimisation, commissioning and process diagnostics. Operators, designers and safety engineers alike are using simulators to familiarise themselves with the plant early during design and training.
There are now many desktop power plant simulators for nuclear, fossil-fuel, landfill gas, energy-from waste, combined-cycle and other plants. There are even respectable PC game-type simulators. To be useful, however, systems need to closely approximate the control environment of the actual power station. Process simulation has to be interfaced to actual control-system operator display consoles with the same process graphics and dynamic response as the actual plant.
Mirroring power fundamentals
The most important requirement is for a simulator to match real-world operation. Kongsberg in Norway bases its plant simulator on the latest block (Block 4) of an oil/coal fueled thermal power plant in Vesteraas, Sweden. The Thermal Power Plant simulator trains and assesses operators in the running of Distributed Control Systems (DCS) and in plant operation, including training in plant start-up and shut-down, emergency situations and safety procedures.
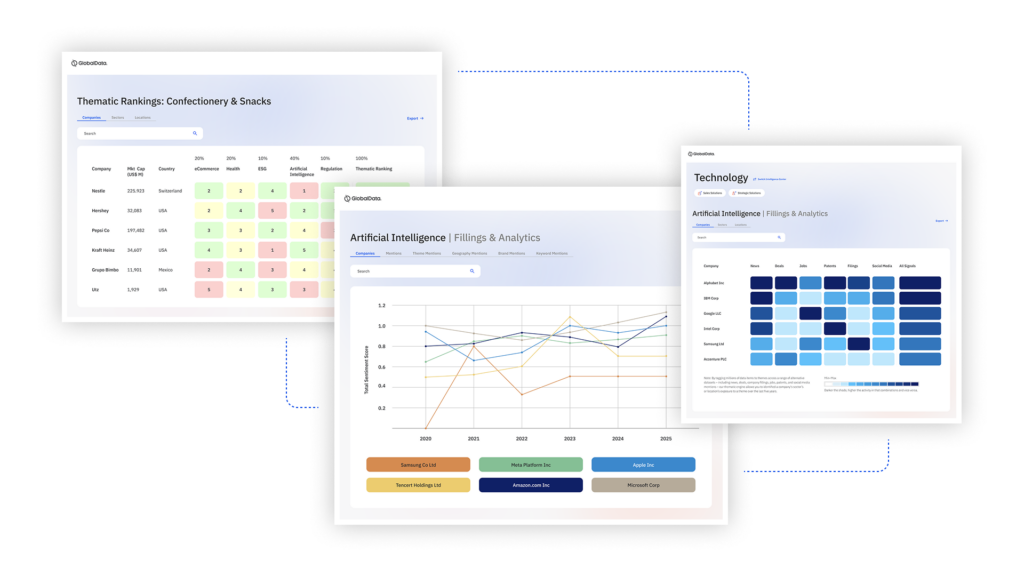
US Tariffs are shifting - will you react or anticipate?
Don’t let policy changes catch you off guard. Stay proactive with real-time data and expert analysis.
By GlobalDataSimulators also need to be part of a structured, consistent training package. Kongsberg has 13 exercises that take trainees through basic first steps such as testing a combustion air-fan, shutting off high pressure feed water pre-heaters and operating feed water pumps. Modules include Boiler Combustion Control, Combustion Air / Flue Gas System, Boiler Water and Steam Systems, Steam Turbines and Electric Generator. They can thoroughly simulate the performance of environmental systems, too, particularly DeNox Plant, SCR Reactors, De-Sulphurisation Plant and Lime Silos.
Using simulators for design verification and optimisation can improve the overall plant design by improving the heat rate and other key process indicators. The software can simulate abnormal incidents and study different approaches to handling them. Operators can learn to identify, diagnose and cure abnormal plant operation. This is particularly important with power plant process diagnostics being such a critical and complex operation. Solutions have to be found in real-time before power can be shut down or public safety is compromised.
Where utilities are replacing older control systems, appliances need debugging and operators need to become familiar with new controls. Cassiopeia Technologies (CTI) reports savings of three weeks in commissioning times for simulators with lower annual outages adding two days of additional full-load generation a year -saving several million dollars.
There are three general stages for building a plant model. Data collection and modeling (stage one) involves entering information from Proportional Integral Derivative controller diagrams, heat balance data, control diagrams, physical data describing component characteristics and operating point data for the desired initial operating conditions. CTI then prepares a task functional flow diagram that identifies each step in the modeling and testing process (stage two). Once the project is complete, it is then documented (stage three).
CTI’s systems can identify differences between monitored and simulated process variables and trigger a search in the customer’s fault-diagnosis knowledge base. For example, it can routinely identify sticking or leaking valves before they are picked up by conventional alarm and monitoring systems.
In turn, system reliability has improved greatly and simulators are now getting the backing of industry associations. In the nuclear industry for example, the International Atomic Energy Agency recommends a Design & Development Performance Analysis Simulator for all countries developing a nuclear programme. CTI has a desktop simulator for CANDU 9 (CANadian Deuterium Uranium 900 MW Pressurised Heavy Water Reactor) using CASSIM (CASsiopeia SIMulation development system).
Making life easier
Open interfaces can greatly extend simulator abilities and Metso Automation’s metsoDNA virtual process controller makes extensive use of this facility. Third-party Windows dynamic process simulation software and Open Connectivity (OPC) interfaces handle data transfer between the virtual process controller and dynamic simulator software. The process control applications are executed in the virtual environment in exactly the same way as in the real system controlling the plant.
I/O connections are transferred through OPC interfaces to the APROS Advanced Process Simulator from the Technical Research Center of Finland. The simulator provides users with a set of predefined process component models. The user selects appropriate process components from model libraries, connects them together and supplies them with process related input data ; all this using a mouse-controlled graphical interface.
The virtual metsoDNA environment has special simulator friendly features such as stopping the execution of the process control application, starting it, saving the complete state of the process control application and loading it back into the operation. These features are used automatically with the same features as the APROS simulation software. This enables the use of several initial process situations, which can easily be loaded into the system for the training of specific control tasks.
The system was used at the Suomenoja district heating power plant with about 1,300 simulated I/O connections. The simulator helped rectify a malfunction in the Forced Draft fan, which had required the plant to shutdown. As it is difficult to shut down this kind of a power station during a disturbance of that kind, the Suomenoja staff practiced the pending shutdown with the simulator. They found that the actual shutdown was almost identical to the simulated one.