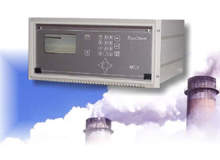
Pollutant monitoring is essential to improve power station performance as much as it is important to ensure compliance with emissions standards and calculating trading allowances. It is needed for ISO-14000 compliance, and is central to the ‘check’ stage of the EPDCA (Evaluate, Plan, Do, Check, Amend/Adopt) improvement cycle for improving plant operations.
Many countries have set limits for the major pollutants released by burning fossil fuels such as carbon dioxide, sulphur oxides, nitrogen oxides and particulates. Simply running the plant under optimum conditions helps reduce pollutant levels but expensive control equipment is often also needed. Either way, exhaust gases need to be monitored. Extractive monitoring used to introduce severe measurement delays that prevented real-time control but semiconductor and other sensors are now allowing real-time continuous emissions monitoring (CEM).
CEM provides a continuous and uninterrupted record of emissions using pollutant analysers. Actual quantities may often be calculated by multiplying pollutant concentrations by volumetric flow rates. These flow rates can themselves be measured continuously, or can be derived from fuel rates if fuel and combustion characteristics are known.
CEM needs to be customised to the plant, with particular attention where gases are sampled from the exhaust stream and transported for analysis. The gases being measured must not be affected by the measurement process, which can be difficult when they contain high temperature and corrosive acid condensates with moisture and particulates. That also means that the monitoring system will often need effective preventive maintenance.
Monitoring the majors
Sensors like Horiba’s INM-700 gas analyser can feed back to control selective catalytic reduction (SCR) systems for NOx emissions. Besides reducing pollutants themselves, sensors like these can detect degraded performance in the catalytic bed.
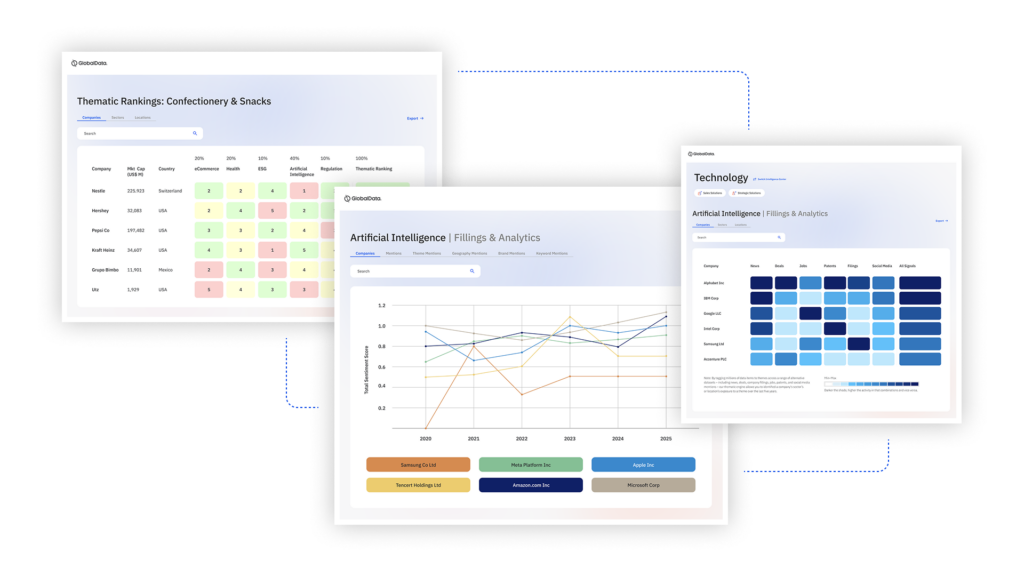
US Tariffs are shifting - will you react or anticipate?
Don’t let policy changes catch you off guard. Stay proactive with real-time data and expert analysis.
By GlobalDataThe INM-700 is a low-maintenance, in-situ instrument with costs low enough for multiple units to be used in-situ at SCR inlets and outlets. The analyser measures NOx levels using a solid-state sensor at the end of an air-cooled probe tube.
It uses a ceramic diffusion filter and zirconium oxide sensor directly in the gas stream. It can be used for inlet SCR control, NOx measurements and burner balancing/combustion tuning in boiler plants.
Rather than dedicate a separate system to each pollutant, multi-component analysers are now simplifying overall systems. EcoChem Analytics’ CEMS uses the ‘HW’ (Hot and Wet) sampling method, maintaining high temperature throughout sampling and analysis. This can directly measure pollutants including NOx, SO2, NH3, HCl and CO2.
The MC3 multi-component IR analyser measures all the gases using just one source lamp, sample cell and detector. Ammonia measurements are of increasing importance as more SCR systems come online. Dual nitrogen oxide analysers have in the past often been unavoidable for detecting the gas using variable converters but these have been expensive and maintenance intensive.
ABB’s ACF-NT is based on an FTIR spectrometer with additional infrared components. The high-selectivity technique measures NOx and SO2 as well as CO, CO2 and Ctotal, O2, HCl, NH3, HF and H2O. The high temperature measurement technique heats the sampling and conditioning systems as well as the measurement cell uniformly to 180°C.
Self diagnostics checks all optics during the daily reference spectrum registration. Any errors are automatically identified, documented and then generate a maintenance request. Calibration procedures have been simplified, with zero and reference points for emissions measurements only needing to be checked once every six months. Users no longer need to maintain an inventory of test gases because a test gas check is only needed twice a year.
Dedicated instruments are still normally needed for some pollutants, particularly for mercury.
Apollo Instruments’ SM-3 CEM Mercury Stack gas monitor measures elemental and particulate mercury, along with bound forms like HgCl2, HgO and HgS. A sample gas stream from the duct is taken through a heated sampling system. The gas is drawn through a high-temperature particulate filter to the reduction unit in the analyser.
In this case, a thermo-catalytic reduction of ionic and bound mercury produces elemental mercury vapour. A maintenance-free peltier cooler dries the gas, with mercury concentration being measured by cold vapour atomic absorption spectroscopy.
Monitoring particulate levels
The prime source of filtration on coal, and also biomass, power stations is often high-efficiency multi-chamber bag houses. PCME’s probe-based Electrodynamic monitoring systems measure the low particulate levels (typically single-figure mg/m3) that escape from the bags.
The systems use a non-contact, charge induction technique. Electrodynamic trending sensors in each compartment of the bag house allow plant operators to observe real-time changes in base line emissions, with real-time leak detection by compartment or row. The system reduces compressed air usage, can predict filter failure, reduces maintenance times/costs and increases the operational life of bag filter elements themselves.
Electrofilters are also widely used on coal-powered power stations and traditionally monitored using opacity instruments. Particulates can build up on the optics, causing reliability and maintenance issues. PCME’s DynamicOpacity Ratiometric Opacity system is less affected by particulate build-up, with ratiometric operation working with lenses that are 90% obscured. The compact transmitter and receiver heads are easy to install and do not need precise laser alignment. A built-in audible alignment aid ensures quick and easy alignment.
Firing gas and oil plants
Although coal- and oil-fired power stations emit most pollutants, emissions from gas-fired systems can rise significantly when running on fuel oils at start-up or under abnormal conditions.
PCME’s PS11 ProScatter has an optical cell with a large representative sampling area for detecting particulate emissions. It has an automated contamination check that eliminates the need for critical moving parts within the instrument – a common source of instrument failure.
The ProScatter measures dust loadings down to 0.1mg/m³ and automatically logs instrument self-checks (zero and span) to allow automatic calculation of statistical averages required by QAL3 (EN-13284-2).
Gas turbines need fabric filters and high-efficiency HEPA filters to provide high-quality air to prevent particulate fouling, erosion and corrosion.
The interspace between these filters can be monitored by PCME’s Electrodynamic Probe Electrification sensors to identify leakage in the primary filter and allow preventative maintenance before the Secondary HEPA filter is blocked or damaged. Properly conditioned inlet air is critical to keep gas turbines operating at peak performance.