
At the United Nations Framework Convention on Climate Change in Mexico in December 2010, world leaders will attempt to come to an international resolution on climate change and the best policies to reverse the environmental damage caused by global carbon emissions.
Although the conference’s spotlight will almost certainly be on the promotion of renewable energy technologies, it is important to remember that traditional fossil fuels are still the world’s dominant source of energy. Increasing efficiency in this area could be the key to making a meaningful impact on emissions in the short term.
According to the World Coal Institute (WCI), improving the performance of the most inefficient coal power stations would reduce global CO2 emissions by as much as 6%.
The following technologies are helping fossil fuel power plants get more for less.
Carbon capture and storage
Carbon capture and storage (CCS), with the potential to reduce plant CO2 emissions by up to 90%, is one of the most promising and most publicised technology in the international push to increase efficiency and reduce emissions. The WCI believes it is the only current technology with the potential to make carbon reductions on the necessary scale. The Intergovernmental Panel on Climate Change has highlighted that CCS could compose more than half of the global carbon reduction effort by 2100.
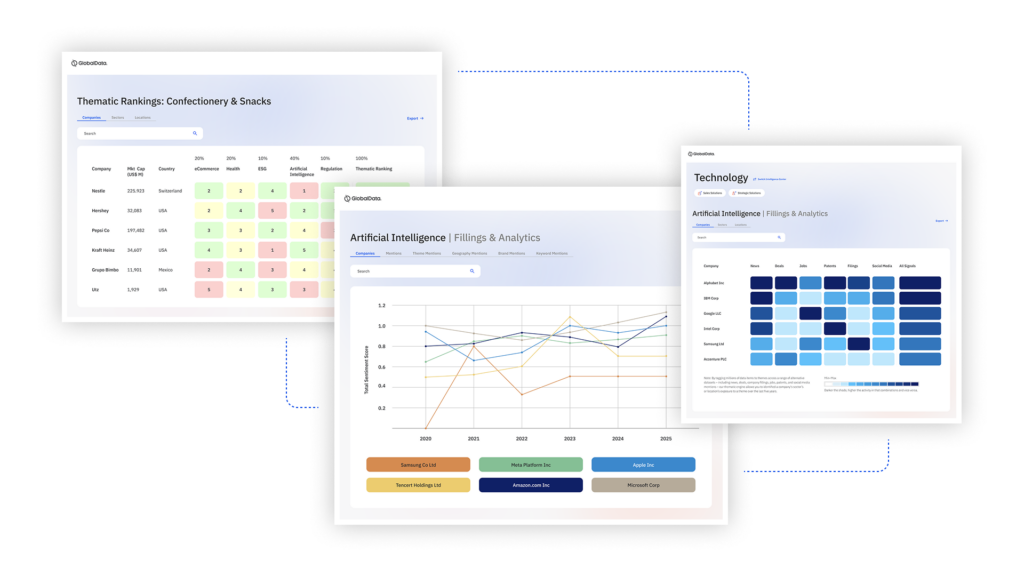
US Tariffs are shifting - will you react or anticipate?
Don’t let policy changes catch you off guard. Stay proactive with real-time data and expert analysis.
By GlobalDataWhether power plants use pre-combustion, post-combustion or oxyfuel processes to capture CO2, the main concern with this technology is the increased energy and cost it takes to implement. In order for plant operators to embrace this technology, it must be refined to reduce costs and make it easier to integrate into operations.
Until then, the number of operational CCS power stations around the world will remain limited to a few environmental role models scattered around the world.
Integrated gasification combined cycle
Integrated gasification combined cycle (IGCC) is another leading technology that is considered too expensive to encourage widespread investment from industry. Despite the costs, the demonstrated benefits are undeniable. IGCC plants convert coal into a synthesis gas called syngas, which is cleaned before being sent to a combined cycle system to generate electricity.
Removing pollutants before the combustion process is significantly more efficient and cost effective than post-combustion removal from exhaust gases, and according to a 2003 statement by GE Power Systems, one of the industry’s IGCC leaders, “the earliest commercial-scale coal IGCC plants are still achieving levels of criteria pollutants lower than those of recently permitted direct combustion plants”.
IGCC technology seals its place in the future of cleaner coal power plants by virtue of its compatibility with CCS. The integrated use of these technologies will be introduced to the world at the Kedzierzyn Zero-Emission Plant in Poland, due to be completed in 2015. The plant will be capable of converting coal to syngas as well as trapping and storing emitted CO2.
The consortium developing the plant has announced that it will be the first power plant to yield negative carbon emissions (-2% CO2). Captured CO2 will either be stored underground or used to produce chemical products including fertiliser, plastics and potentially even synthetic fuels.
Continuous emissions monitors
If the key to emissions reduction is firm state regulations and industry compliance, then continuous emissions monitoring (CEM) systems are vital for relaying reliable emissions data to plant operators and inspectors. CEM systems generally operate by extracting and diluting flue gas samples before being funnelled to a gas analysis system to be tested for pollutants.
The Electric Power Research Institute’s (EPRI) research portfolio for 2011 identifies some important issues for CEM technology. First is the need for widespread expansion in the range of gaseous pollutants measured. Over and above CO2 emissions, power plants are coming under increasing pressure to measure particulate matter, nitrogen oxides (NOx) and acid gases.
As coal-fired power stations are the largest man-made source of mercury emissions, continuous mercury monitors (CMM) are also being developed as a dedicated tool to help utilities comply with performance standards for mercury output.
Selective catalytic reduction
Many fossil fuel power stations have invested in selective catalytic reduction (SCR) systems to reduce emissions of NOx, which contribute to global warming and acid rain, as well as hampering plant growth and damaging crops. The process involves the injection of ammonia or urea into the flue gas stream to convert NOx into diatomic nitrogen or water.
SCR systems require a high level of precision to efficiently convert NOx (SCR systems can convert 80-90% of a power station’s NOx) and to avoid the release of unreacted ammonia, known as ammonia ‘slip’. As with many efficiency technologies, a prohibitive factor for SCR is the expense involved with installation, especially when retrofitting the technology into unprepared plants.
SCR is following the general industry trend of technology integration in order to keep costs as low as possible. In February 2010 Paragon Airheater Technologies announced that its new DuraTEC enamel coating, which is used to protect regenerative airheaters from corrosion, can also make use of embedded SCR technology to further reduce NOx emissions.
“This additional catalyst layer is capable of cost effectively reducing the quantity of NOx emissions from a power plant beyond that of the SCR that is already in place,” said John Guffre, Paragon’s chief research scientist.
Thermal efficiency: from subcritical to supercritical
Studies suggest that there is a gulf of nearly 20% between the efficiency of average and state-of-the-art pulverised coal combustion plants. Much of this can be explained by the increased use of supercritical steam cycle technology in modern plants.
Operation at higher temperatures and pressures achieves higher efficiencies that have the potential to provide power companies with a quick ROI to cover the initial cost of installing new boilers and turbines.
R&D activities being conducted in countries such as Japan, Germany and Denmark have highlighted that the next step in thermal efficiency – ultra-supercritical units – could further increase efficiency to around 50%, a huge improvement over the current average of 28%.
The WCI has predicted that breakthroughs in this research will lead to a significant boom in the installation of supercritical and ultra-supercritical technology in coal-fired plants around the world.