
Any prize for the “most elegant” wind generator design would likely go to the Darrieus rotor. At its simplest, it has a vertical central rod with an aluminium strip attached each side at top and bottom. When the wind blows, the rotor spins. Unlike other vertical axis generators (which are mainly used for pumping water or grinding), it can compete with horizontal axis machines for generating electrical power.
Unfortunately, the conventional Darrieus rotor has low starting torque and so doesn’t start on its own, can suffer pulsating stresses, and also becomes unstable if it is too tall. It has therefore never really made it to mainstream production.
A V-shaped version of the design, however promises to solve those problems. Invented by aeronautical engineer David Sharpe, it has been developed by the NOVA (novel offshore vertical axis wind turbine) project at Cranfield University.
Two arms project out from the base of the Aerogenerator, with wind catching the sails at the end of the arms to generate lift and turn. In operation, the Aerogenerator mimics a spinning sycamore leaf. The structure uses techniques developed for semi-submersible oil platforms and is inherently suited to maritime use: it floats, there are few moving parts, and the weight is concentrated at the base to give a low centre of gravity. It could therefore reduce the costs of deepwater offshore wind energy.
The Aerogenerator has other advantages over horizontal axis machines. It is insensitive to wind direction, so doesn’t need gearing mechanisms to turn it into the wind. The generator and gearbox are at the bottom of the structure, and easy to reach for maintenance. Half the height of an equivalent horizontal-axis turbine, the Aerogenerator is less visible from a distance, and interferes with radar less than taller horizontal axis turbines.
It is also more easily scalable than horizontal axis machines. For a start, horizontal axis machines need large towers. As the blades turn, gravity subjects them to a changing stress (compressed when rising, stretched when falling) that repeats for every rotation – up to 20 times a minute. Increasing the blades’ thickness increases their weight and also the stress placed upon them.
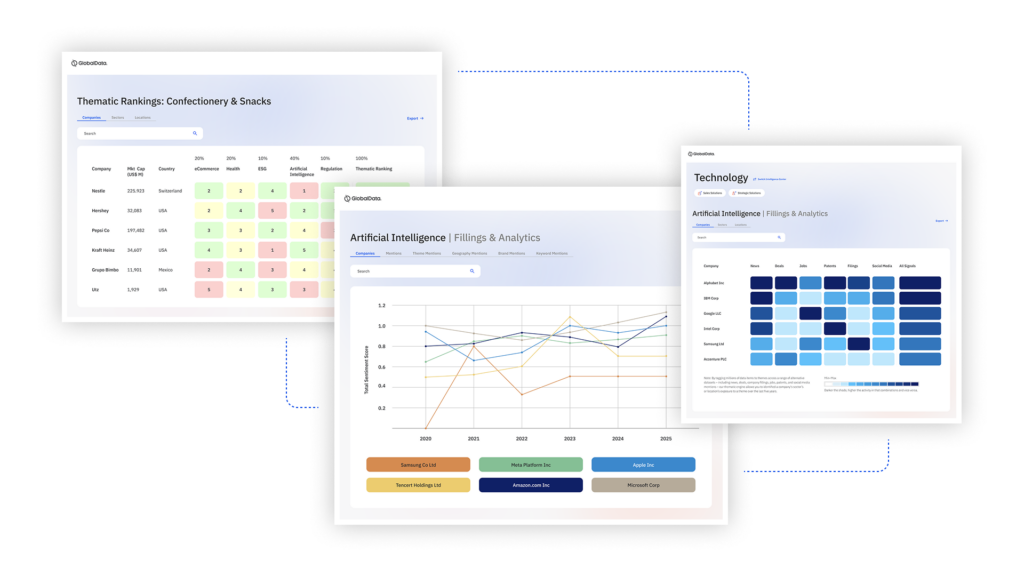
US Tariffs are shifting - will you react or anticipate?
Don’t let policy changes catch you off guard. Stay proactive with real-time data and expert analysis.
By GlobalDataIn fact, the whole drive train needs to be stronger to cope with the heavier components. Since this is located inside the nacelle, at the top of the tower, it increases the height of the centre of gravity. In contrast, the blades of the Aerogenerator are relatively small and lightweight, and so suffer less fatigue.
Steady improvements – the design riddle
The conventional Darrieus turbine was patented in the US in 1931 and resembles a huge two-bladed egg beater. Vertical axis machines were developed in the US and Canada in the 1970s in response to the oil crisis, with Sandia National Laboratories eventually developing a 625kW 34m diameter research machine. Following the global triumph of short-term thinking when the oil prices dropped again, the research was largely abandoned.
see 40GW installed by 2020.”
The NOVA project has taken up where the US research left off. The six-year project is funded by the ETI Partnership, with the detailed design now approved. Contributors include Cranfield University (aeronautic structural and materials, and offshore support structure), Sheffield and Strathclyde Universities (drive train and power systems), QinetiQ (aerodynamic performance), the Centre for Environment, Fisheries and Aquaculture (environmental impact), James Ingram & Associates (offshore wind farm development) and OTM Consulting (project management).
Wind tunnel tests have demonstrated a 5kW Aerogenerator, and early designs planned a 144m-high structure generating up to 5MW. Recent improvements have doubled the estimated power of the Aerogenerator X to 10MW while halving the weight. A full-sized version is now being built by a cooperative effort at Arup, Rolls-Royce, BP, Shell, Grimshaw and Cranfield University. The first machines will stretch around 275m from blade tip to tip and should be built by 2014. According to Theo Bird, founder of Wind Power Limited, the design should scale up to 20MW or more. The company also foresees underwater versions of the Aerogenerator to derive power from waves and tides.
European rivals from Norway, the Netherlands and Denmark
The increased cost of steel and other materials has been pushing up wind power project prices, and getting the electricity to where it is actually used is costly. Offshore farms can take advantage of stronger and steadier winds than onshore, though, so can generate up to 50% more energy, and there are fewer problems with visual impact. The Gunfleet Sands and Robin Rigg wind farms have, in 2010, helped the UK to become the first country to install above 1GW of offshore power. There is great activity in Europe particularly, and the European Wind Energy Association would like to see 40GW installed by 2020.
Wind Power is hoping for a large slice of this market but will be competing against other large offshore wind generators now in development. Most promising are those from Statoil / Norsk Hydro and Sway AS in Norway, Blue H Group in the Netherlands and Floating Power Plant in Denmark. All use horizontal axis turbines, and all float on the sea surface.
of the Aerogenerator are relatively small and lightweight.”
Two of the systems have a long underwater section to keep the generator buoyant so that it bobs in the water like a fishing float. Statoil is now testing its 2.3MW Hywind generator, which has a steel cylinder jacket filled with water as ballast. It extends 100m beneath the sea surface and is attached to the seabed by three anchor piles. It uses a 65m-high Siemens turbine with an 82.4m rotor diameter. Also from Norway is Sway, which is also tethered to the seabed and floats downwind. Sway has partnered with Areva-Multibrid to adapt its 5MW turbine.
The other two systems use floating platforms. The Blue H Group’s SDP (submerged deepwater platform) has a buoyant steel body, which is held semi-submerged under water by chains. The chains keep the body constantly tensioned by a counterweight on the sea floor. A prototype has been under test since 2007, and the first commercial turbines are now being constructed. The Floating Power Plant’s Poseidon is interesting because the floating foundation carries a wave generator as well as wind turbines. The wave power is converted by pistons with hydraulic take-off, and a plant 230m across could carry three commercial wind generators to generate a total of 20MW.