
Amec Foster Wheeler was awarded the contract by Fusion for Energy (F4E), the EU organisation responsible for Europe’s contribution to ITER, which is the world’s biggest fusion energy project. The company’s system, officially known as the Neutral Beam Cell Remote Handling System, is the largest nuclear robotics contract awarded by F4E to a UK company to date.
Amec Foster Wheeler will lead the project with support from a host of other specialists, including the Culham Centre for Fusion Energy (the UK’s national fusion research laboratory), Reel SAS of France and Walischmiller Engineering GmbH of Germany.
As the project begins to move through the concept phase along its lengthy path, Jon Montgomerie, chief engineer at the European Remote Handling Alliance (ERHA), an Amec Foster Wheeler co-operative contracting arrangement, discusses the origin of the idea and how it will work in practice.
Gary Peters: Can you talk me through Amec Foster Wheeler’s expertise in the area of using robotics for energy and nuclear fusion?
Jon Montgomerie: The nuclear fission industry has used remote handling in one form or another right from its inception, as it was known from the start that there were some situations where materials handling requirements could not be met safely using a human operator with conventional tools. Gradually, technology has evolved to better meet these needs, starting with simple tongs operated through a ball joint in a shielding wall up to the electronically controlled robotic devices we are developing today. This specialised sphere of expertise can be called nuclear remote handling (RH) or robotics, and we have a number of experts in this field with expertise and past experience of nuclear RH work.
The company itself has delivered quite a few projects over the years in nuclear RH, with a rise in recent years partly fuelled by an increase in remote interventions needed by one of our major clients to address emergent issues, often age-related, with its fleet of nuclear power stations. In recent years, Amec Foster Wheeler’s nuclear business has had an average turnover in Nuclear RH of around £5m per year, so the Neutral Beam Remote Handling System contract, at €70m over seven years, represents a major step forward for us.
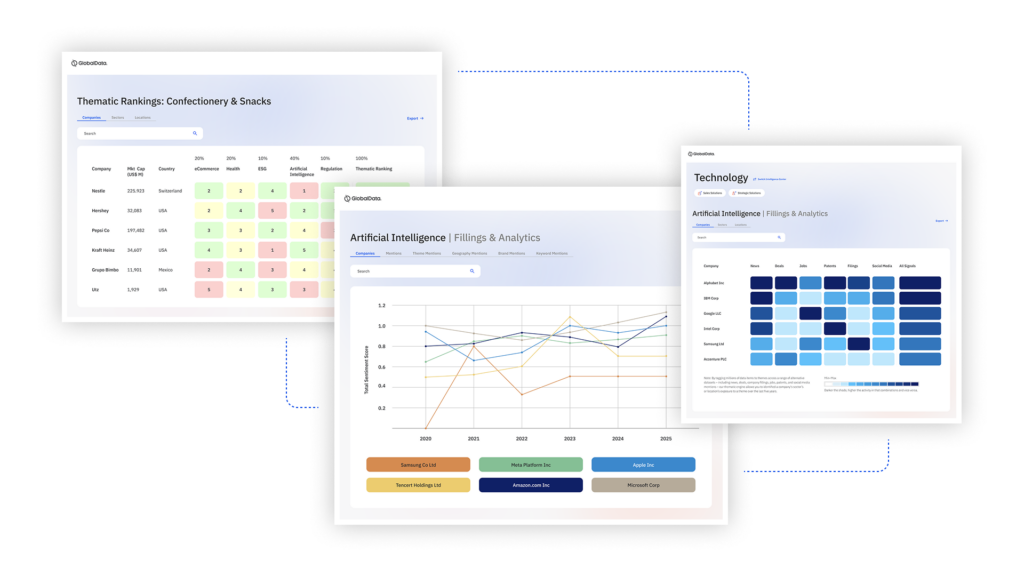
US Tariffs are shifting - will you react or anticipate?
Don’t let policy changes catch you off guard. Stay proactive with real-time data and expert analysis.
By GlobalDataGP: How did the premise of a remote handling system for the ITER fusion reactor in France come about?
JM: ITER will, in very simple terms, recreate the reaction that is going on in the centre of the sun held within a vacuum and constrained by large magnetic fields. This creates an environment that personnel cannot access, and therefore remote handling systems need to be created to allow all sorts of tasks to be performed. The Neutral Beam Remote Handling System is one of these systems. Concepts for these various systems have been developed for a number of years by the scientific community, and we are now at the stage of the ITER project of taking these concept designs and making them real, so that they can actually be built.
GP: Digging deeper into the specifics, how will the system be operated?
JM: Over the projected seven-year development and delivery phase, ERHA will need to involve hundreds of people with skills ranging from those of the project director through to the specialist engineers with skills in robotics, lifting systems, specialist cutting and other tool systems, control system, vision systems, and so on, right through to the craftsmen delivering the precision manufacturing necessary to build this type of equipment and then safely and successfully install and commission it.
Seventy-five academics have called for a larger role for nuclear in the future energy mix.
Once installed and commissioned, the system will be operated by ITER staff, trained by us, working from a control room safely shielded from the environment of the Neutral Beam cell, and about 100m away from it. All operations will be not only carried out remotely but also viewed remotely; that is to say, there will be no direct view through windows or whatever. Monitoring operations will be entirely by CCTV and other electronic monitoring systems.
Interestingly, from our past experience we know that even the humble microphone can be a hugely valuable instrument in allowing RH operators to understand what the equipment is doing and how it is performing, but there will of course be many more sophisticated instruments generating data to guide the operators in their work.
GP: What will be the core responsibilities of the system?
JM: As the name implies, the Neutral Beam Remote Handling System works in the Neutral Beam Cell, providing for all maintenance activities to be carried out from – and including – the opening of the shielded covers on the neutral beam lines.
Each of these lines – there will be three or four – is around the size of a small bus, and is crammed with complex equipment working at up to a million volts. Provision needs to be made to disconnect and change out the various modules inside that allow the beam lines to work. Essentially it must be possible to completely strip out the entire contents of the beam line vessels to an empty shell and then re-assemble completely, all without any man-access to the cell.
Common to most other nuclear RH systems, it must also be possible to recover from any postulated fault scenario, again without any ‘man access’ to the cell, so each machine needs systems designed into it for recovery, and methods for remotely changing over to them so that a failed piece of equipment can be retrieved remotely and repaired.
GP: What benefits will it provide?
JM: Essentially it would be impossible to operate the Neutral Beam Cell without the RH system, and without the NB cell it would be impossible to operate ITER.
There are several other systems in the plant that have a similar essential nature, in that the areas they work in are entirely non-accessible, yet contain components and systems vital to the functioning of the ITER plant.
GP: What challenges exist when trying to develop a remote handling system for such a task?
JM: It is obviously our prime intention to utilise existing technological building blocks wherever possible – we don’t want to re-invent the wheel! All the same, there are some specific technical issues that are new or at least somewhat novel, and an early part of the work is to identify these and carry out the necessary R&D to convert these ‘technical uncertainties’ into tried and tested technology that we can deploy with confidence. This is particularly crucial for ITER because, to a greater extent than most other nuclear plants, it will be hugely dependant on its Remote Handling systems, some of which – if they failed – could bring the whole plant to a standstill.
In particular, there are a number of tools that need to be developed for the robots to deploy, for the remote cutting, welding and inspecting of pipework, all to a very high standard. Remote cutting and welding have been done before, but the challenges of difficult access, constrained space, limited connectivity and extremely high standards to be achieved mean that these tools will need to be absolutely cutting-edge.
On a macro scale, the deployment of the robot systems and their tools requires deployment machines with reach distances and number of degrees of freedom that are rare even with relatively simple RH systems. These systems must reach a long way into awkward spaces and achieve a very high quality of work; all in all, a fairly challenging nuclear environment.
GP: How will the remote handling system help demonstrate the technical feasibility of nuclear fusion as a future power source?
JM: The feasibility of fusion as an energy source will be verified by the functioning of the ITER experiment itself, and ultimately proven by the follow-up plant DEMO, which will be the world’s first prototype Fusion Power Station. But, as noted before, certain aspects of the functioning of the ITER plant would be impossible without the sophisticated RH systems we are working on, and as such they are part of that proof that fusion can, in the end, provide a sustainable energy source for the future.
GP: How important are developments such as these to nuclear fusion and indeed energy as a whole?
JM: The successful functioning of these RH systems is vital to the operation of the ITER plant itself, and their successors will be equally vital to the operation of DEMO, and hence to the very future of fusion as a viable energy source.
More broadly, since the working environments are similar, there is huge potential for the technology, knowledge and experience generated on these projects to transfer back into the fission industry from where almost all the expertise originally came.
The more extreme challenges posed by the ITER Remote Handling systems is forcing nuclear RH technology forward at a much accelerated pace, making new approaches then available to [the] wider nuclear industry, potentially improving efficiency and effectiveness in all kinds of other applications. We already have a small R&D contract in support of Fukushima, and this is just one example, albeit a well-known one, of where improvements in nuclear remote handling and robotics could have huge benefits.