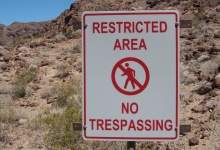
Nuclear power stations are home to considerable amounts of radioactive materials, yet the most common hazards confronting plant personnel aren’t radiation-related, they are risks found at most large industrial facilities. These include heat stress, falling, electrical shock, toxic chemicals and confined space entry.
The nuclear power industry is considered a relatively safe industry to work in, with lost work-time incidences and fatalities falling. The Union of Concerned Scientists’ Dave Lochbaum, a nuclear engineer with 17 years’ experience in the nuclear power industry, most of which was operating plant sites, says years ago worker injuries and fatalities were viewed as “part of doing business” but today they are “signs of business done badly”.
The World Association of Nuclear Operators’ (WANO) 2012 performance indicators report, the industrial safety accident rate, tracks the number of accidents worldwide that result in lost work time, restricted work or fatalities. It announced a drop from 5.20 accidents per 200,000 work hours in 1990, with 169 stations reporting, to 0.68 accidents per 200,000 work hours in 2012 with 195 stations reporting.
Although this trend shows an impressive improvement, fatal accidents still occur. Last year at the Arkansas Nuclear One plant, an employee died and eight other workers were injured after a 525t stator fell as it was being lifted by a temporary crane. The US Department of Labor’s Occupational Safety and Health Administration (OSHA) cited many of the companies involved, including Siemens Power Generation and Entergy Operations, for safety violations. Events such as this demonstrate the importance of avoiding complacency.
Creating a safety and reporting culture
Related feature
Hinkley Point C nuclear plant: a good deal for the UK?
The UK Government struck up an unprecedented deal with EDF Energy to build two new nuclear reactors at Hinkley Point C. But is it really a good deal for the UK?
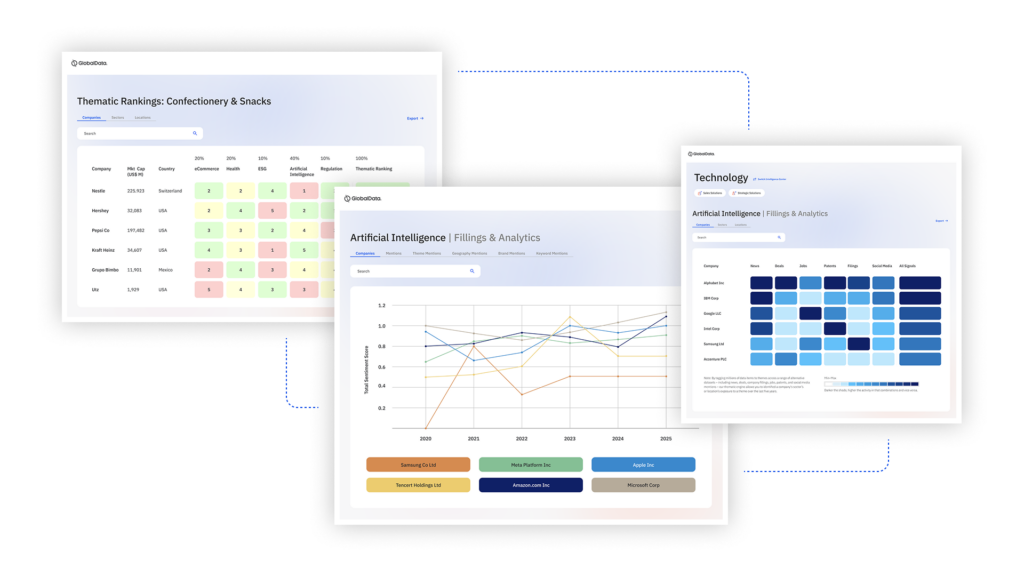
US Tariffs are shifting - will you react or anticipate?
Don’t let policy changes catch you off guard. Stay proactive with real-time data and expert analysis.
By GlobalDataWANO managing director Ken Ellis says complacency is a risk once a high level of safety performance is achieved.
“For those charged with the enormous responsibility of ensuring the world’s reactors operate safely, that means constantly challenging ourselves to be better,” he says.
One way to sustain a high safety record is for the operator to ingrain a health and safety culture into its workforce so good practice is carried out as a matter of course.
Head of technical safety and support at Torness nuclear power station in Scotland, Ross McAllister, says: “To me safety isn’t just about what you do at work, it’s how you impact staff in their values and attitudes and their behaviour.”
He says the EDF-run Torness plant has recently passed five years since the last lost time incident on-site and is about to reach the milestone of 2,000 days since the last lost time incident with contractors on-site. The second-generation power plant has between 700 and 1,000 staff on site at any given time.
In 2013, the plant achieved a total recordable injury rates (TRIR) rate of 0.6, which McAllister says is an industry benchmark. To achieve such a good safety record, as well as following UK power plant safety guidelines and training, McAllister encourages an open reporting culture.
“We positively recognise people’s reports,” he says. “Every day we have a condition report of the day, which encourages people to raise events adverse to quality or safety. We also encourage people to raise positive observations if they see something that is good practice.”
The plant compiles daily, weekly and monthly condition reports, which the data of is trended to identify issues that frequently arise. McAllister says the company cannot deal with everything reported but those reported frequently, however small, will be addressed. For example, he says the coveralls worn by employees were redesigned after a high occurrence of reports that the zip kept breaking.
This reporting culture is regularly praised and McAllister says the plant has a ‘roaring trade of iPods’ being handed out as another form of reward.
“We do make errors and mistakes so we do need to employ tools and techniques to mitigate the likelihood of that happening and mitigate any potential outcomes that would lead to,” he explains.
International culture of share and learn
Just as it is important to record health and safety events, it is equally important to share these experiences across the industry so that everyone can learn from one another’s mistakes rather than having to learn from trial and error themselves, says Lochbaum.
As example, Lochbaum highlights how a recent report by the Institute for Nuclear Power Operations (INPO) showed an increasing number of hand injuries during refuelling outages. Exelon, which operates the largest number of nuclear reactors in the US, used the report to train its workers on better safety techniques. As a result, the company’s rate of hand injuries was nearly halved from the rate in a prior refuelling outage.
In the US, Lochbaum says the sharing of international information to improve occupational health and safety in nuclear power plants could perhaps be improved.
“The overwhelming majority of information shared internationally about nuclear safety involves technical issues, proper designs and prudent maintenance,” he says. “Some of the shared information covers non-technical issues like training programmes for workers. But the fitness for duty requirements and broader worker safety issues are seldom if ever subject to information exchanges. That seems flawed.”
WANO encourages the sharing of information within the industry, and believes the nuclear power sector is unique in the energy field because of its openness with such information.
“By openly sharing our experiences, we have shed the perceived shackles of competition in the shared pursuit of increased safety,” Ellis says.
McAllister says Torness is involved in this open sharing of information, engaging with INPO in the US and WANO to submit reports of near misses, events and good practice, which are shared worldwide. The plant also participates in peer reviews, where employees go to other plants around the world to review their operations and provide them with challenges on how they can improve their safety culture.
The plant’s workers also receive information themselves and, for example, in the case of the Arkansas Nuclear One event, McAllister says they wouldn’t necessarily look at only the physical things that went wrong but also the operational issues. “What was the leadership and manager like?,” he says. “What are the processes like that allowed that to happen and are there any similarities like that [at Torness]? How can we learn from that?”
Technology to aid fallible humans
Technology can also be a powerful defender against health and safety violations and remove workers from potentially dangerous situations.
McAllister says Torness uses remote operating techniques such as cameras and equipment on the end of umbilicals, allowing workers to access hazardous areas of the plant without having to physically be there. The plant uses seawater as part of its conventional processes and carries out inspection of subsea areas using a submarine with a special camera, which means divers don’t have to be sent down into a potentially dangerous environment.
Another method used at nuclear reprocessing site Sellafield in Cumbria, England, is Human Recognition Systems’ MSite, MTrust and MSkills technology. Together, they use biometrics, such as iris and finger print recognition, to ensure only correctly trained and adequately qualified people can access certain areas of the plant.
Human Recognition Systems founder and CEO Neil Norman said: “It’s a zero-tolerant system and that is what health and safety should be. It only takes one slip-up, one mistake or error and then before you know it you have a massive fallout.”
The MSkills system builds, manages and maintains worker profiles to ensure they are fully aware, equipped and accredited and are up-to-date with their training. If the systems shows that they have missed anything, the MSite part of the technology will block their entrance to site, meaning if they haven’t attended safety talks or updated their training then they are left unable to work.
Technology may offer certain benefits but it too isn’t infallible, as Ellis warns. “Technology certainly assists in safety and plays a very key role, but we must never underestimate the importance people play when they interface with machines,” he says.
Always room for improvement
It seems the nuclear power industry has worked hard to improve occupational safety for its workers and has made some excellent progress. However, as has been widely acknowledged, the industry should never ease up and allow its incident figures to creep back up.
One particular area Lochbaum finds troubling is the issue of worker impairment due to fatigue. This is an area that is hard to combat with technology, regulation and a solid health and safety culture. Even if you set maximum working hours, it is impossible to police what employees do in their spare time. For example, an employee could be exhausted from having their sleep disturbed by their newborn child. Tired workers are more likely to make mistakes.
“It’s a problem we are seeking to resolve here [in the US], but it’s complicated,” Lochbaum says. “If the Nuclear Regulatory Commission ruled tomorrow that workers could not put in more than eight hours in any day or 40 hours in any week, people have pointed out that workers would respond by getting two jobs so as to have the income they want.”
It is certain that there will always be anomalies such as these that prove harder to monitor than other health and safety issues. They will need to be worked out, as well as keeping up the job of maintaining and improving the health and safety standards already achieved.
“We will never say our work is done,” Ellis said.