GE Renewable Energy has announced a research partnership with Fraunhofer IGCV and voxeljet to develop the world’s largest 3D printer for offshore wind applications.
As part of the project, the partners are developing a large-format 3D printer capable of producing sand moulds to cast metal parts for use in an offshore wind turbine nacelle.
How well do you really know your competitors?
Access the most comprehensive Company Profiles on the market, powered by GlobalData. Save hours of research. Gain competitive edge.
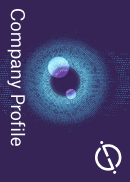
Thank you!
Your download email will arrive shortly
Not ready to buy yet? Download a free sample
We are confident about the unique quality of our Company Profiles. However, we want you to make the most beneficial decision for your business, so we offer a free sample that you can download by submitting the below form
By GlobalDataThe project is intended to streamline the production of key components of GE’s Haliade-X offshore wind turbine by printing moulds for cast components.
The three companies intend to launch the project in the third quarter of this year, with initial printer trials set to begin in the first quarter of next year.
GE Renewable Energy senior additive design engineer Juan Pablo Cilia said: “The 3D printed moulds will bring many benefits including improved casting quality through improved surface finish, part accuracy and consistency.
“Furthermore, sand binder jet moulds or additive moulds provide cost savings by reducing machining time and other material costs due to optimised design.”
GE claims the technology can reduce the time taken to produce patterns and moulds from ten weeks to two weeks.
The 3D printer is currently in the development phase. Its development is being backed financially by the German Federal Ministry for Economic Affairs and Energy.
Fraunhofer Institute for Casting, Composite and Processing Technology director Prof Dr Wolfram Volk said: “We aim to optimise the mould printing to avoid extremely costly misprints or even miscasts, to save on [the] binder and activator and to improve mechanical and thermal behaviour during casting.
“By developing a process that conserves resources as much as possible, we want to help to improve the environmental and cost balance in the manufacture of wind turbines.”
Earlier this week, GE Renewable Energy secured planning approval for an offshore blade manufacturing facility in Teesside, UK.