
Netherlands-based offshore contractor Seaway Heavy Lifting (SHL) has selected British engineering company Atkins to design jacket substructure and foundations for the 588MW Beatrice Offshore Windfarm (BOWL) development in the outer Moray Firth, UK.
The deal is a part of SHL’s engineering, procurement, construction, and installation (EPCI) contract with BOWL, which is a partnership between SDIC Power, SSE Renewables, and Copenhagen Infrastructure Partners.
Atkins’ offshore wind deliver director Andy Thompson said: "This is a very exciting project for us as it underlines our ability to design jacket structures for the latest turbines in deep water.
"This capability compliments our ability to design XL monopiles for the latest turbines, floating structures, and fixed offshore substations."
"The project approach adopted by SHL and BOWL has allowed Atkins to develop the design from concept, through front end engineering and design (FEED), and into detailed design along with other vital members of the Beatrice supply chain."
Under the terms of the deal, Atkins will install 84 jacket substructures and other related foundations for the 7MW turbines provided by Siemens. Substructures will be deployed at different water depths up to 55m.
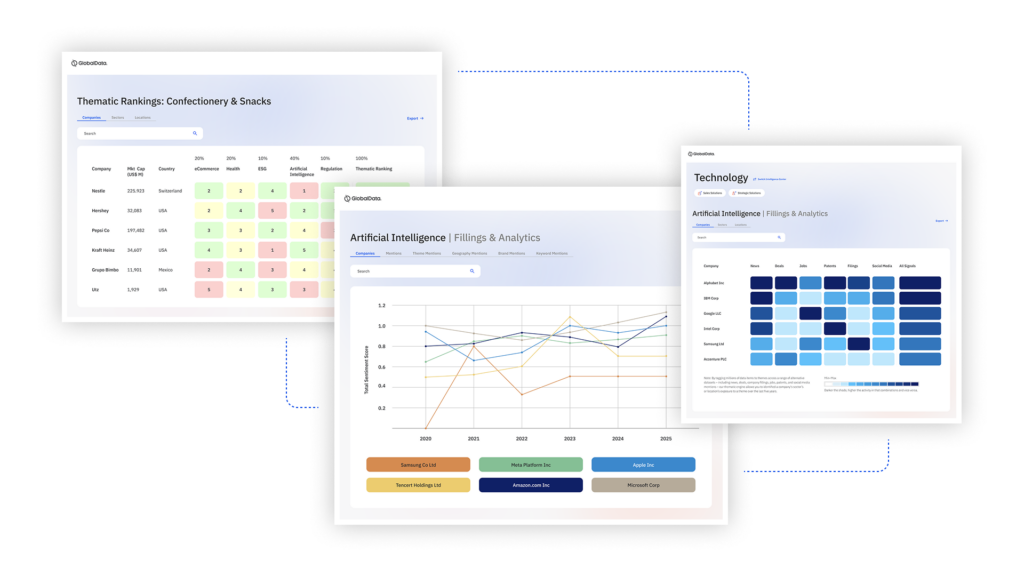
US Tariffs are shifting - will you react or anticipate?
Don’t let policy changes catch you off guard. Stay proactive with real-time data and expert analysis.
By GlobalDataThompson added: "Drawing on years of jacket design experience in oil and gas and as an industry-leading offshore wind team, we’re designing the first mass-produced deep water jacket substructure for an offshore windfarm.
"The evolution of the jacket substructure in this way is enabling savings on steel, fabrication, and installation costs as we are developing a lighter, simpler, and highly standardised substructure."
Image: Beatrice Offshore Windfarm in the outer Moray Firth, UK. Photo: courtesy of SSE.