

UK-based company Carbon Trust’s Offshore Wind Accelerator (OWA) has launched a new project to reduce offshore wind costs by optimising jacket foundation designs through enhanced fatigue standards and validation of faster testing and fabrication methods.
Entitled ‘Improved Fatigue Life of Welded Jacket Connections (JaCo)’, the new £2.4m project aims to create an improved understanding of fatigue performance by testing full-size jacket nodes developed from existing manual and novel automated welding processes.
Jacket foundations are used for offshore wind projects as monopiles are not practical enough for several future offshore wind facilities that are located in deeper water sites and are equipped with larger turbines.
The Scottish Government-funded JaCo project will run for more than three years and is being supported by major offshore wind developers, Scottish Power Renewables, Dong Energy, Statoil, EnBW and Vattenfall.
Belgian material research centre for the application of steel (OCAS) will use advanced testing techniques developed in-house in order to cut the time required to complete fatigue tests.
As a project coordinator, Carbon Trust will work in collaboration with OCAS and industry partners to ensure programme delivery, which includes numerical analysis, accelerated testing and sourcing of nodes.
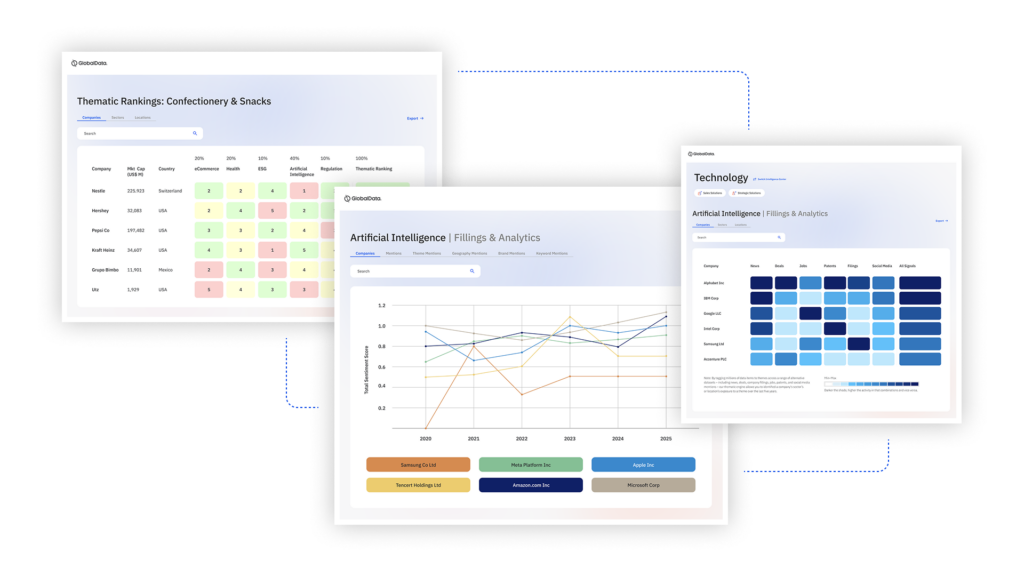
US Tariffs are shifting - will you react or anticipate?
Don’t let policy changes catch you off guard. Stay proactive with real-time data and expert analysis.
By GlobalDataCarbon Trust Offshore Wind director Jan Matthiesen said: “With an increasing trend of larger turbines that will be installed in deeper waters, we will see a growth in the use of more economic jacket structures.
“We have launched this project to drive cost reductions by optimising such structures. In addition, this project will aim to demonstrate the performance of robotic welding, which will allow the supply chain to fabricate at industrial scale.”
Jacket foundation technology comprises mainly of welded tubular space frames fabricated in carbon steel. Each welded connection point is deemed a node.
Being a major design consideration, fatigue at these welds often proves to be the limiting factor.
OCAS’s testing method works on resonance testing at an increased test frequency of typically 20Hz, quickening delivery of results considerably within 14 days for a full-scale jacket node.
The current project is expected to validate the use of what are anticipated to be less-conservative fatigue S-N curves for offshore wind turbine jacket foundations compared with the present practice.
Testing of several manually and automatically welded nodes, along with enhancements in production techniques and optimised fatigue curves are expected to reduce the weight of jacket foundations and lower both capital expenditure (CAPEX) and installation costs.
Image: Carbon Trust OWA’s Improved Fatigue Life of Welded Jacket Connections (JaCo) project. Photo: courtesy of Carbon Trust.