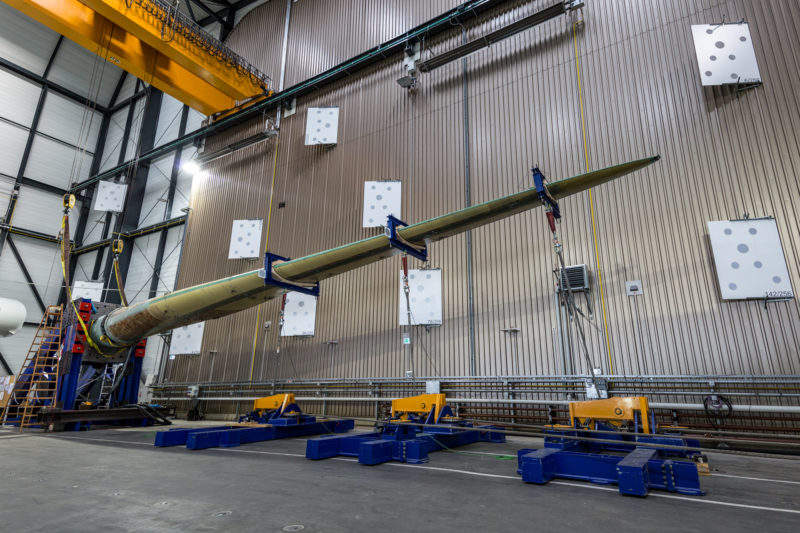
The Fraunhofer Institute, a German organisation which specialises in applications for emerging technology, is developing a rotor blade for wind turbines that can rotate in response to wind pressure for more efficient operation.
The SmartBlades2 project involves the German Aerospace Centre and Wind Energy Research Alliance, and puts into practice blades designed and simulated as part of the SmartBlades1 project.
In conventional wind turbines, blades that experience sudden and very strong gusts of wind are often turned away from the wind for their own protection, counterintuitively meaning the turbine produces no electricity when winds are at their strongest. There is also significant variation in pressure on individual blades; a turbine with blades 85m long sweeps an area of 22,670m2, creating a space large enough for individual blades to experience different pressure.
The new blades use bend-twist coupling (BTC) to rotate on their own axes in response to variations in wind pressure. The prototype blades are 20m long and their tips are slightly offset, to the rear in the direction of rotation.
“The use of BTC blades on wind turbines in the development stage makes the turbine lighter compared to a turbine with conventional blades, due to the reduced load on the structure,” the Fraunhofer Institute announced.
“This, in turn, means a drop in material and logistics costs while maintaining the same energy yield. In existing turbines, the use of BTC blades allows the rotor diameter to be increased without having to strengthen the other turbine components.
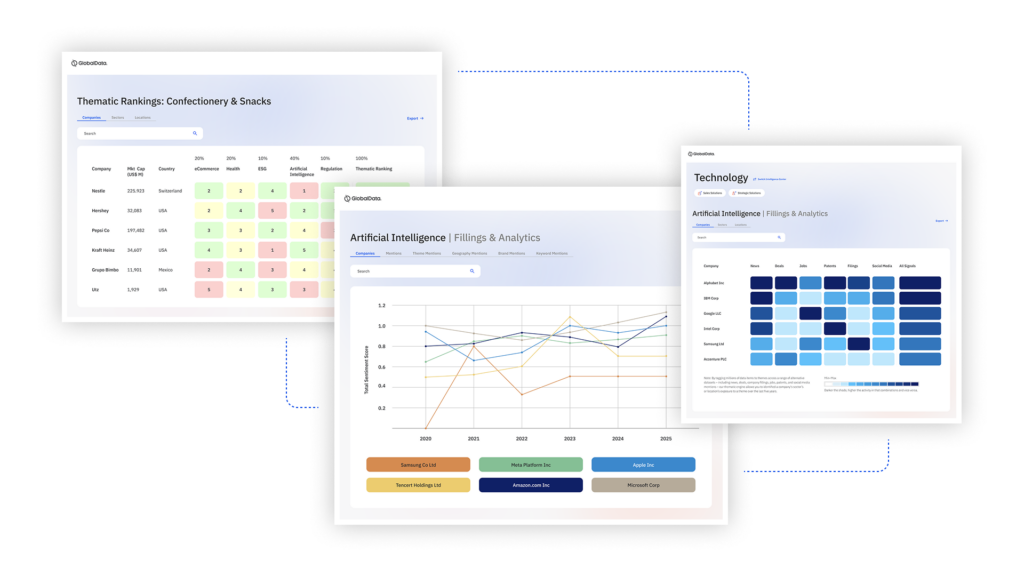
US Tariffs are shifting - will you react or anticipate?
Don’t let policy changes catch you off guard. Stay proactive with real-time data and expert analysis.
By GlobalData“This results in an increase in revenue thanks to a greater wind yield.”
The blades are being tested in Bremerhaven to measure their durability and to what extent they deform when subjected to high pressure. Deformation will be measured along three axes of each blade, and angle sensors will precisely measure the direction of force applied. The blades will also be subject to fatigue testing, where the stresses incurred over a 20 year lifespan of a blade are simulated within a shorter timeframe.
Following these tests, the blades will be tested further in the Rocky Mountains in the United States.
“The aim of the accompanying measuring campaign is to determine whether the load reduction thanks to BTC seen in the simulation can be recreated under real-life conditions and whether its effect is as pronounced as expected,” said the Institute.
The blades were designed by Dr Elia Daniele, and received €15.4 million in funding from the German Federal Ministry for Economics Affairs and Energy.