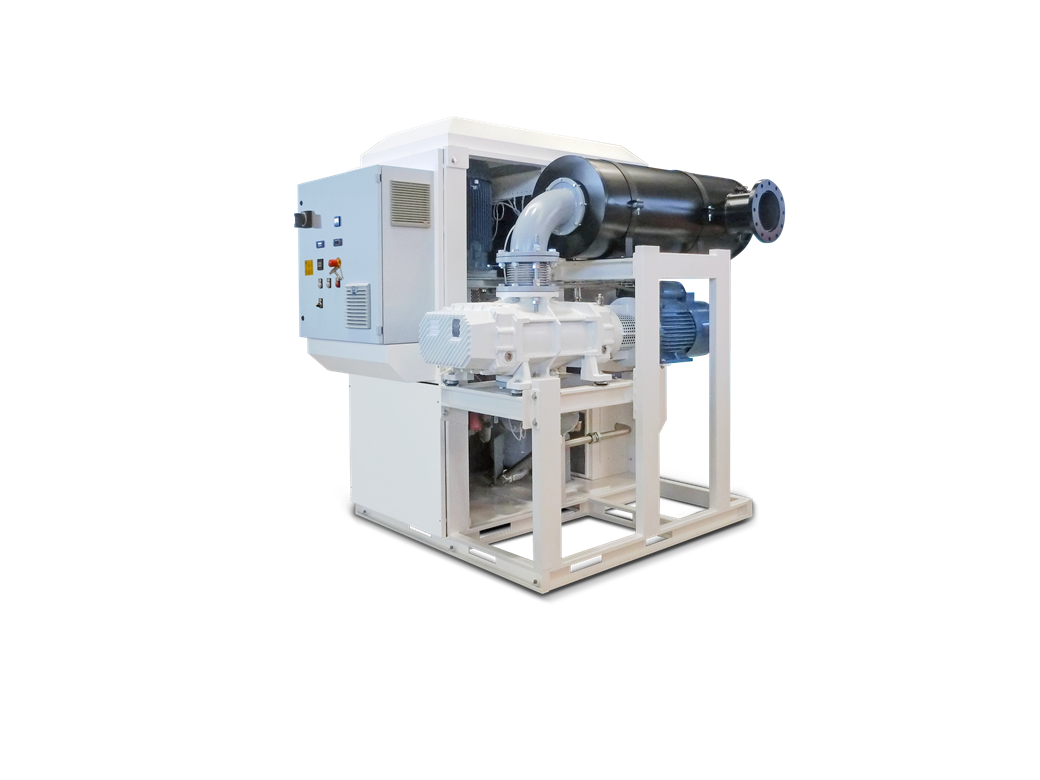
Pipeline systems, often stretching over thousands of kilometers and varying in diameter, require thorough cleaning and drying before gas introduction. Whether in remote locations, refineries, or offshore installations, effective moisture removal is critical to prevent contamination and ensure long-term system integrity. Leak testing under pressure is standard, but the choice of drying technique has a decisive impact on efficiency, cost, and operational readiness.
Operators often default to familiar technologies, but field experience shows that drying speed, mobility, energy efficiency, and investment cost must all be considered when selecting the most appropriate method.
Drying with hyper-dry air relies on large oil-free compressors connected to chillers to reach dew points around -40°C. This setup demands high energy input, generates considerable waste heat, and occupies significant space. Even when executed properly, it may fail to reach water dips and dead-ends within the system, leaving moisture that compromises pipeline performance.
Nitrogen, appreciated for its inert properties, is used especially in hazardous environments like refineries. Although it absorbs water vapor effectively, nitrogen must be compressed and forced through the pipeline, requiring expensive logistics for on-site generation or delivery. It is also ultimately released into the atmosphere, adding to operational complexity.
Vacuum drying offers a more efficient and reliable alternative. By reducing the pressure inside the pipeline, water evaporates at lower temperatures and is continuously removed as vapor. This method requires substantially less energy than compressed-air or nitrogen systems and is highly mobile and adaptable to field conditions. Vacuum drying systems using high-capacity pumps can handle several hundred kilograms of water vapor per hour, making them ideal for large or complex pipeline networks.
Since 2007, Pneumofore has delivered vacuum systems specifically engineered for pipeline drying, based on its century-long expertise in rotary vane technology. These multi-stage systems, often air-cooled for deployment in hot climates, combine robust performance with low operating and investment costs. Pneumofore’s vacuum solutions are among the very few, if not the only one, capable of reliably evacuating hundreds of kilograms of water vapor per hour without compromising equipment durability.
With decades of field data and case studies, Pneumofore is uniquely positioned to support pipeline drying projects with precise drying time calculations. Operators are invited to consult with Pneumofore to evaluate how vacuum drying can shorten drying time, reduce costs, and outperform conventional methods in both speed and reliability.