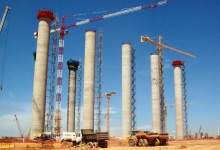
It typically takes ten years to build a coal-fired power station, but South African state utility Eskom made a bid to build the new Kusile facility in Mpumalanga Province in just eight. The plant’s first unit is set to be in commercial operation before the end of 2014, and will provide much-needed relief for the country’s strained power supply.
In order to fast-track the $14bn plant, Eskom used 3D plant simulator technology developed by US-based Bentley. Prototype 3D visualisation and simulation technologies were used to create a virtual 3D plant for use in operations and maintenance, as well as staff safety training.
Eskom’s domestic deployment of this technology to build the six-unit, 4,800MW plant has seen the team honoured with an award at the Bentley Systems 2013 Be Inspired Awards in October 2013 and named as one of Future Power Technology magazine’s Ones to Watch for 2014.
Eskom’s Riekie Swanepoel, who took the lead on the 3D simulation project, explains the project’s success.
Heidi Vella: Tell us about your work on the Kusile Power Plant.
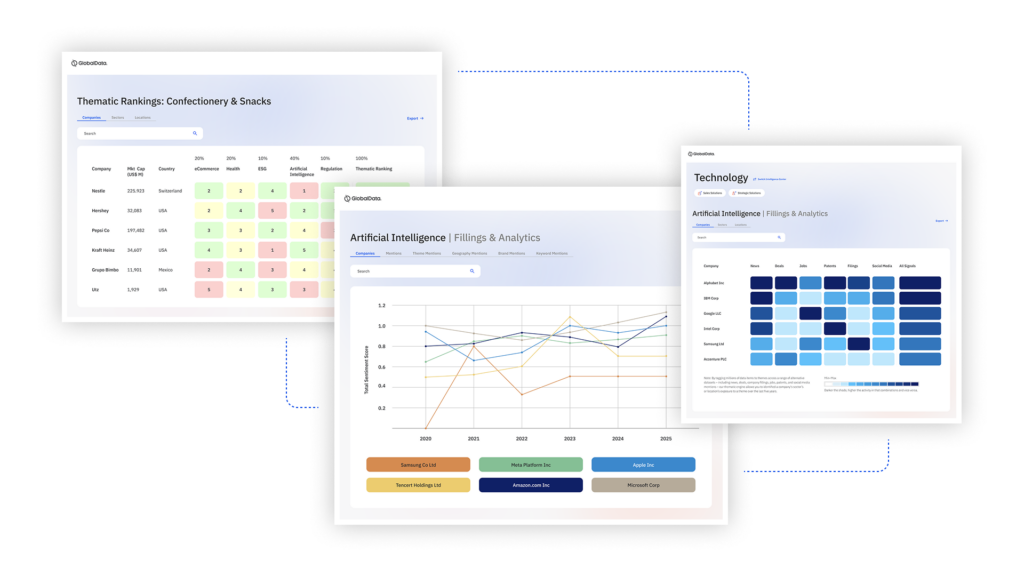
US Tariffs are shifting - will you react or anticipate?
Don’t let policy changes catch you off guard. Stay proactive with real-time data and expert analysis.
By GlobalDataRiekie Swanepoel: The intent was to create a 3D visualisation platform that enabled better engineering, construction, operating and maintenance of the plant asset.
This 3D Operations and Maintenance (O&M) Simulator project was run in parallel with the EPC [engineering, procurement and construction] work underway at Kusile Power Station.
The 3D Simulator project operated in tandem with the general design and construction activities, but we were allowed interaction with the Kusile Project team to source the 3D information required to build the simulator model and to clarify any design base issues.
Activities also included conversion of conventional 2D P&ID [piping and instrumentation diagram] drawings and information to an intelligent data-centric format. This was done with the bigger picture in mind of having a plant 3D virtual information portal where the 3D model becomes the ‘window’ into all engineering and other asset information and data.
HV: What challenges did you need to overcome during the project?
RS: The biggest challenge was the rapidly changing design base. Although the plant construction has already started, portions of the plant are still in detail design phase, with the result that there are regular changes to the design 3D model.
For O&M purposes, one has to have a 3D virtual model that mimics the actual ‘as built’ plant, so it becomes mission-critical to keep up-to-date with design updates and changes and to ensure that 3D model submissions accurately reflect updates or changes to the design.
This challenge was overcome by having an arrangement with our Kusile Implementation Partner, Black & Veatch, to supply Eskom with the latest copy and version of 3D models from the various EPCs on the project on a monthly basis.
Changes to 3D model submission methodology (by the EPCs) and comparative file analysis capability was implemented to more easily identify changes to 3D model files submitted, allowing the CADD [computer-aided dynamic design] office team to hone in and focus on only those plant areas where changes have taken place.
HV: The remote avatar training aspect of the project is quite unique…
RS: Yes, indeed. When we started looking at the 3D model deliverables, it soon became evident that many stakeholders only saw this as a project deliverable to be ‘ticked off’ at the end of the project. Our team started asking: ‘What more can be done with this 3D model and just how much can this be leveraged for value across the entire plant asset lifecycle?’.
We came across CAVE [cave automatic virtual environment] technology, but a big inhibitor of this technology was cost, as well as the fact that it is limited to a single location.
So we started asking: ‘What if we can take the plant 3D model to the operator/maintainer/engineer at his/her computing device, and create a virtual plant world for them to interact with anytime, anywhere?’ And, even better, allow the staff to become a part of the virtual plant, being able to interrogate and interact with the plant interactively. Enabling this capability took a number of months, and included ‘rendering’ of the CADD 3D model into more photo-realistic textures to create a ‘real plant’ look and feel.
Because we could use gaming technology, it was possible to create a ‘real-life’ experience, while making sure the speed with which the avatar can walk the plant closely relates to actual average human speed of walking. Inclusion of dynamic simulation further enhanced the user experience as we could then start looking at creating scenarios, for example, a fire or steam leak in the plant, to which the user-avatar must react.
Being able to ‘walk’ the plant like you would do in real-life has increased our ability to look at plant design from an operability and maintainability aspect very early on in the design cycle, as knowledgeable operating and maintenance staff know what things to look for when it comes to these aspects.
HV: How does it feel to receive recognition for your work?
RS: It certainly feels great, especially within the context of Eskom’s vision to drive towards being one of the top five utilities in the world. This recognition shows the Eskom Group Technology Engineering team is committed and capable in assisting Eskom to achieve this vision.
Recognition always inspires a team to keep up the good work, and working with the Kusile Project team has been an empowering experience, it showcases what is possible when human energies and capabilities are harnessed together to deliver power generation infrastructure and bleeding-edge innovation like this.
HV: What is Eskom up to now and in the future?
RS: Eskom is currently focused on building Medupi, Kusile and Ingula Power Stations, but also has a number of renewable energy project initiatives underway, which are in various stages of project maturity.
Ingula Power Station is pumped storage (hydro), and Eskom is also actively looking at wind energy and solar energy plants (PV and CSP types). These projects are in line with Eskom’s commitment to increase its focus on more sustainable energy generation. There are also a number of refurbishment projects in progress on existing plants and infrastructure.
Image: courtesy of Eskom.
Related content
The power of simulation
There are now many desktop power plant simulators for nuclear, fossil-fuel, landfill gas, energy-from waste, combined-cycle and other plants.
Future Power Technology: BRICS Edition
Future Power Technology takes a look at the power industry in the BRICS nations.